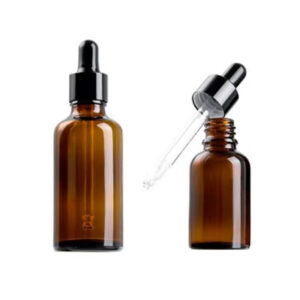
News & Blog
Great things in business are never done by one person. They’re done by a team of people. We have that dynamic group of peoples
Glass containers play a crucial role in various industries, especially in cosmetics, perfumery, and pharmaceuticals. While they offer elegance, durability, and protection, quality defects in manufacturing can compromise their performance and aesthetic appeal. In this article, we explore common glass container defects, their causes, and potential solutions.
Glass manufacturing is a complex process, and various defects can occur due to raw material issues, mold design flaws, or improper forming techniques. Below are the most common defects encountered:
Bubbles are air pockets trapped within the glass structure. They can appear due to:
Impurities in raw materials
Inadequate melting or refining
Poor batch composition
Impact: Aesthetic imperfections and reduced structural integrity.
Cracks are visible fractures, while checks are fine fissures on the surface. Causes include:
Sudden temperature changes during production
Improper annealing process
Mechanical stress during handling
Impact: Increased risk of breakage, making the product unsafe for use.
Glass containers with inconsistent wall thickness can result from:
Poor mold design
Uneven distribution of molten glass
Incorrect forming process
Impact: Structural weaknesses, leading to breakage under pressure.
Foreign particles embedded in the glass, such as unmelted sand or refractory materials, can arise due to:
Contaminated raw materials
Incomplete melting process
Furnace lining erosion
Impact: Aesthetic flaws and potential weak points that increase breakage likelihood.
These defects occur due to:
Friction during transportation or storage
Improper handling
Rough contact with machine parts
Impact: Reduced visual appeal and possible structural damage over time.
Issues such as rough finishes, misaligned necks, or improper sealing surfaces are caused by:
Faulty mold designs
Inconsistent glass distribution during forming
Poor trimming and finishing processes
Impact: Leakage issues, improper closure fit, and reduced customer satisfaction.
Manufacturers implement stringent quality control measures to minimize defects and ensure high-quality glass containers. Key strategies include:
Improved Raw Material Selection: Using high-purity materials to minimize impurities and bubbles.
Optimized Furnace Operations: Ensuring complete melting and refining to avoid stones and inclusions.
Mold Maintenance: Regular inspection and upkeep of molds to maintain consistency.
Advanced Forming Techniques: Implementing precise forming and cooling techniques to prevent thin walls and cracks.
Surface Treatment: Applying coatings or polishing methods to reduce scratches and enhance durability.
Automated Inspection Systems: Utilizing high-tech inspection tools to detect and eliminate defective units before packaging.
Defect Type | Causes | Impact |
---|---|---|
Bubble Defects | Impurities, inadequate melting, poor batch composition | Aesthetic flaws, weak structure |
Cracks and Checks | Sudden temperature changes, poor annealing, mechanical stress | Increased breakage risk |
Thin/Uneven Wall Thickness | Poor mold design, uneven glass distribution | Structural weakness, potential breakage |
Stones and Inclusions | Contaminated raw materials, incomplete melting | Aesthetic issues, weak points |
Surface Scratches & Abrasions | Friction, improper handling, rough machine contact | Reduced durability and appeal |
Sealing and Finish Defects | Faulty mold design, inconsistent glass distribution | Leakage, improper closure fit |
Understanding and addressing quality defects in glass containers is essential for maintaining product integrity, aesthetic appeal, and customer satisfaction. By implementing robust quality control measures and continuous improvements in the manufacturing process, businesses can ensure the production of premium glass containers that meet industry standards.
Whether you are a manufacturer or a brand seeking reliable packaging solutions, partnering with experienced suppliers with strict quality assurance processes can significantly impact your productโs success in the market.
Discover the top 10 woods for perfume caps, comparing texture, pros, cons, and price to help you choose the best material for stylish, high-quality packaging.
Explore the sustainability of glass packaging, its recyclability, and environmental benefits.
Discover 10 expert tips to choose the best cosmetic bottles, ensuring quality, durability, and sustainability while enhancing your beauty routine effortlessly.
Discover the world of reed diffusers & essential oils! Learn how to choose the best glass bottle, reeds, & oils for creating a relaxing aromatic home.
Explore the electroplating process for cosmetic glass packagingโits principles, advantages, materials, coatings, and applications for enhanced beauty and durability.
Explore custom vs. stock bottles for skincare packaging. Learn how Yafengโs solutions boost brand identity, quality, and efficiency in this in-depth guide.
Discover how gradient color spray transforms cosmetic glass bottles, enhances brand image, and boosts product appeal with expert insights from Yafeng Packaging.
Discover how rattan aromatherapy works and why glass bottles are the best choice for long-lasting scent, safety, and sustainable, elegant packaging.
Discover the top 10 woods for perfume caps, comparing texture, pros, cons, and price to help you choose the best material for stylish, high-quality packaging.
Explore cosmetic glass bottlesโsafety, eco benefits, types, coloring, mold costs, MOQ, and production tipsโin one expert, data-rich guide.
Discover how to ensure high-quality silk screen printing on cosmetic and glass bottles with expert testing methods, defect analysis, and reliability standards.
WhatsApp us