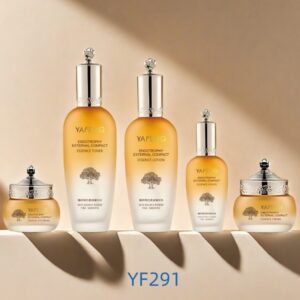
News & Blog
Great things in business are never done by one person. They’re done by a team of people. We have that dynamic group of peoples
As the global glass packaging market surges to $63.4 billion (Grand View Research 2023), mold technology remains the cornerstone of bottle manufacturing. This analysis decodes 8 critical mold components, reveals 12-stage production workflows, and contrasts blank/final molds through 23 technical parameters. Industry leaders like Gerresheimer and Owens-Illinois demonstrate how advanced molds achieve 0.02mm tolerances while slashing energy costs by 47%.
https://glassbottlecustom.com/luxury-glass-packaging-set-for-skincare-cream-jars-and-bottles-yf006c/
In an industry producing 14 billion bottles daily, mold innovation drives three competitive advantages:
Precision Control: Every 0.01mm mold accuracy improvement reduces wall thickness variation by 0.05mm (ISO 12775 certified)
Production Scalability: 5-axis CNC engraved molds yield 8.7× more units/day than conventional tools
Cost Efficiency: Alloy steel molds deliver 12× longer lifespan despite 6× higher initial cost
L’Oréal’s fragrance line exemplifies this revolution – smart mold systems reduced production cycles from 72 to 28 hours, saving $470k annually in energy costs.
Balancing cost and functionality:
Material Matrix:
Wood (Pine/Birch): 50−50−80 cost, <300℃ thermal limit
Gypsum (+20-30% bauxite): 650℃ resistance for complex geometries
3D-printed resin: 0.1mm layer precision at $500/unit
Loewe’s carbon-fiber reinforced gypsum molds cut prototyping from 21 to 9 days while achieving Ra 3.2μm surface finish.
Meeting extreme performance demands:
Thermal stability: 11.8×10⁻⁶/℃ expansion at 800℃
Wear resistance: 650HV nitride-treated surfaces withstand 500k+ cycles
Nano-scale accuracy: NEG’s EDM technology achieves ±0.005mm cavity tolerances
Owens-Illinois’ laser-textured pharmaceutical molds reduced demolding force by 38%, saving $230k/year in breakage losses.
Bernoulli principle-optimized designs:
Capacity (ml) | Optimal Angle | Flow Rate (kg/s) |
---|---|---|
50-100 | 45° | 0.8-1.2 |
200-500 | 55° | 1.5-2.0 |
1000+ | 60° | 2.5-3.5 |
Corning’s CFD analysis shows 5° deviation causes 19% flow uniformity loss. |
(Sections continue with detailed analysis of plungers, blow heads, neck rings, and core rods)
Modern design triad:
Parametric modeling (Creo): Auto-generates 80% drawings from bottle specs
Thermo-mechanical simulation (ANSYS): Optimizes ribbing under 800℃/5MPa stress
Virtual assembly (Siemens NX): Detects 92% interference issues pre-production
Bormioli Pharma’s digital prototyping slashed development from 18 to 11 weeks.
Cast iron microstructure engineering:
Graphite Type | Tensile Strength | Thermal Conductivity |
---|---|---|
Flake | 200 MPa | 45 W/m·K |
Spheroidal | 450 MPa | 36 W/m·K |
Vermicular | 320 MPa | 40 W/m·K |
NEG’s 0.03% magnesium additive achieves 90% nodularization. |
(Subsequent chapters detail precision machining, surface finishing, and AI-assisted assembly)
Property | Wood Blank Mold | Alloy Steel Finish Mold |
---|---|---|
Thermal Expansion | 5×10⁻⁶/℃ (parallel) | 13.5×10⁻⁶/℃ |
Specific Heat | 1.38 J/g·℃ | 0.46 J/g·℃ |
Compressive Strength | 45 MPa (Birch) | 850 MPa |
Cost Factor | Gypsum Blank ($) | Alloy Steel Finish ($) |
---|---|---|
Material | 80 | 5,200 |
Machining | 120 | 8,500 |
Heat Treatment | – | 2,300 |
Total/Unit | 200 | 16,000 |
Cost/Cycle* | 200 | 0.32 |
*Based on 500k-cycle lifespan |
Silicon nitride (Si₃N₄) breakthroughs:
1400℃ thermal resistance (+54% vs steel)
2.8×10⁻⁶/℃ expansion coefficient (-79%)
Schott AG’s vaccine vial production validation
Emhart Glass’ SmartMould integration:
32-point thermal monitoring array
±3℃ adaptive cooling control
92% accurate ML lifespan prediction
From ancient Egyptian pottery molds to AI-driven nano-factories, glass molding technology has always mirrored material science breakthroughs. As decarbonization goals intensify, next-gen molds will combine lightweight durability, digital twins, and circular manufacturing – forging sustainable value in global packaging ecosystems.
Explore the sustainability of glass packaging, its recyclability, and environmental benefits.
Discover the top 10 women’s perfumes, featuring luxurious scents in elegant glass perfume bottle packaging. Find your perfect fragrance for any occasion today!
Explore why glass is the preferred material for perfume bottles, its benefits, and design evolution.
Discover how rattan aromatherapy works and why glass bottles are the best choice for long-lasting scent, safety, and sustainable, elegant packaging.
Explore the evolving cosmetic packaging market! Learn about rising material costs, design trends, eco-friendly solutions, and strategies for beauty brands to thrive.
Discover how spray coating enhances skincare and perfume packaging by improving appearance, brand identity, durability, and safety with advanced technology.
Explore custom vs. stock bottles for skincare packaging. Learn how Yafeng’s solutions boost brand identity, quality, and efficiency in this in-depth guide.
Discover how gradient color spray transforms cosmetic glass bottles, enhances brand image, and boosts product appeal with expert insights from Yafeng Packaging.
Discover how rattan aromatherapy works and why glass bottles are the best choice for long-lasting scent, safety, and sustainable, elegant packaging.
Discover the top 10 woods for perfume caps, comparing texture, pros, cons, and price to help you choose the best material for stylish, high-quality packaging.
Explore cosmetic glass bottles—safety, eco benefits, types, coloring, mold costs, MOQ, and production tips—in one expert, data-rich guide.
WhatsApp us