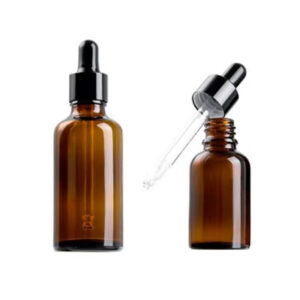
News & Blog
Great things in business are never done by one person. They’re done by a team of people. We have that dynamic group of peoples
This article deeply explores the surface electroplating process of cosmetic glass packaging, and elaborates on its principles, advantages, main materials, coating types, process flow and specific applications in the cosmetics industry. Through rich data, cases and chart analysis, it fully demonstrates to readers how this key process can improve the visual effect and durability of cosmetic glass packaging, helping cosmetic brands stand out in the market.
Electroplating can form a new and extremely glossy metal layer on the surface of metal and non-metal parts. Taking cosmetic glass packaging as an example, the original ordinary glass material, after electroplating, presents a mirror-like gloss. In a survey on consumers’ preferences for cosmetic packaging, more than 80% of respondents said that cosmetic packaging with a high-gloss electroplated surface can attract their attention more. This high-gloss metal layer directly improves the visual grade of the original parts, making cosmetics more dazzling on the shelves and attracting consumers’ attention. Compared with directly forming parts with metal, the cost of electroplating is much lower. For example, the cost of using pure metal to create a lipstick shell may be 3-5 times that of electroplating a glass lipstick shell. Through electroplating, cosmetic brands can achieve high-end visual effects at a lower cost.
Electroplastic plating of specific areas on the surface of the same part has great flexibility. In cosmetic packaging, we can use special waxes and coatings to apply to areas that do not need electroplating to achieve electroplating effects in some areas. For example, on some cosmetic tool components, only key decorative parts are electroplated, which not only highlights the design focus but also saves costs. Chromium electroplating is widely used in surface treatment of transportation and furniture industries due to its excellent wear resistance and glossiness, and is also favored in the cosmetic packaging industry. In the design of lipstick shells, chromium electroplating can create a stylish and durable appearance and enhance the texture of the product.
There are about 30 types of electroplated metals, and the most widely used ones are zinc, cadmium, copper, nickel, chromium, silver, tin, gold, iron, cobalt, lead, antimony, platinum, titanium, rhodium, etc. In addition to single metal plating, there are many alloy platings, such as copper-tin, copper-zinc, copper-nickel, nickel-iron, lead-tin, zinc-tin, zinc-iron, zinc-nickel, copper-cadmium, zinc-cadmium, tin-iron, tin-cobalt, tungsten-iron, etc. Different metal and alloy platings have different characteristics and are suitable for different cosmetic packaging material requirements. For example, the zinc plating layer has good anti-rust performance and is often used in some cosmetic bottle caps that are cost-sensitive and require certain protection; the copper plating layer has good conductivity and decorative properties and can be used for the electroplating of some cosmetic tool components.
In terms of plastics, ABS is the most commonly used. This is because ABS can withstand high electroplating temperatures of 60°C (140°F), and its electroplated and non-electroplated layers have high bonding strength. In plastic accessories of cosmetic glass packaging, such as some plugs and gaskets, ABS materials are not only greatly improved in appearance after electroplating, but also more tightly bonded to glass packaging. Most metals can be electroplated, but different metals have different levels of purity and electroplating efficiency. Among the common electroplated metals, tin, chromium, nickel, silver, gold and rhodium each have their own characteristics. Rhodium, as a type of platinum, is extremely expensive and can maintain high brightness for a long time. It can resist most chemicals and acids. It is most commonly used in products with extremely high requirements for product surface gloss, such as trophies and medals. It is also occasionally used in high-end cosmetic packaging to highlight the luxurious quality of the product. It should be noted that nickel metal cannot be used for electroplating products that come into contact with the skin, because nickel is irritating and toxic to the skin, which is an important consideration when choosing electroplated metals for cosmetic packaging.
Electroplated metal | Features | Applicable scenarios | Is it suitable for contact with the skin |
---|---|---|---|
Tin | Low cost, has certain rust resistance | Some accessories for low-end and mid-range cosmetic packaging materials | Yes |
Chromium | Good wear resistance, high gloss | Lipstick shell, makeup tool components | Yes |
Nickel | Magnetic, moderate cost | Not for contact with skin products | No |
Silver | Good conductivity, gorgeous appearance | High-end cosmetic packaging decoration | Yes |
Gold | Precious, strong antioxidant | High-end cosmetic packaging embellishment | Yes |
Rhodium | High brightness, chemical corrosion resistance | Top luxury cosmetic packaging materials | Yes |
According to the plating, it can be divided into chrome plating, copper plating, cadmium plating, tin plating, zinc plating, etc. Different plating has different characteristics and uses. The chrome plating layer has good hardness and wear resistance, and its surface is bright. It is often used for cosmetic packaging materials that require high hardness and beauty, such as the handles of some high-end makeup brushes. The copper plating layer is often used for electroplating of some cosmetic tools that require conductivity, such as the contact parts of some electric beauty instruments, because of its good conductivity and low cost.
During electroplating, the plating metal or other insoluble material is used as the anode, and the workpiece to be plated is used as the cathode. The cations of the plating metal are reduced on the surface of the workpiece to be plated to form a plating layer. In order to eliminate the interference of other cations and make the plating uniform and firm, a solution containing the plating metal cations is used as the plating solution to keep the concentration of the plating metal cations unchanged. Taking the common ABS plastic parts electroplating as an example, ABS electroplating is to chemically corrode the B (butadiene) in ABS, so that the surface of the product presents some loose pores, and then a layer of conductor (such as copper) is attached to make it conductive, and then electroplating is performed in accordance with the metal electroplating method. Therefore, ABS electroplating is a mixture of chemical plating and electroplating. This unique process enables plastic materials to have metal-like appearance and performance, greatly expanding the design possibilities of cosmetic packaging materials.
Pretreatment includes grinding, preparatory cleaning, water washing, electrolytic degreasing, water washing, acid impregnation and activation, water washing and other steps. Grinding can remove defects and rough parts on the surface of glass packaging materials, so that the subsequent electroplating layer can adhere better. In a study on the factors affecting electroplating quality, it was found that the adhesion of the electroplating layer of finely ground glass packaging materials increased by 30%. Preparatory cleaning and water washing steps remove impurities such as dust and oil on the surface, preparing for subsequent electrolytic degreasing. Electrolytic degreasing can more thoroughly remove stubborn oil stains and ensure the cleanliness of the packaging surface. Acid impregnation and activation are to activate the surface of glass packaging materials and enhance the bonding with subsequent coatings.
The neutralization step is used to adjust the pH value of the packaging surface and create a suitable environment for electroplating. The electroplating process is divided into base plating and surface plating. Base plating forms a basic plating layer, which provides a good adhesion foundation for subsequent surface plating. Surface plating selects a suitable metal plating layer according to design requirements to create the final appearance effect. After the electroplating is completed, the residual plating liquid on the surface is removed by water washing and pure water washing, and then dehydration and drying are carried out to ensure that the surface of the packaging material is dry to prevent rust and corrosion. In the cosmetic packaging industry, because the coating after electroplating cannot be in direct contact with the contents, the electroplating process is mainly used in external components, such as various packaging shells, lipstick shells, bottle cap shells, makeup tool components, etc. [Here you can insert a schematic diagram of the electroplating process to show the order and relationship of each step]
As a popular category in cosmetics, the attractiveness of lipstick packaging is crucial. Electroplating technology is widely used in lipstick shells. Through chrome plating, copper plating and other processes, lipstick shells present a fashionable and high-end appearance. According to market data, lipstick products with electroplated lipstick shells have a sales volume 20% – 30% higher than lipsticks with ordinary packaging. Consumers are more willing to pay for lipsticks with exquisite appearance, and electroplating technology has improved the market competitiveness of lipstick brands.
After electroplating, the bottle cap shell not only has a more refined appearance, but also has significantly improved durability. For some high-end cosmetics brands, electroplated bottle caps can better reflect the high-end positioning of the brand. Makeup tool components such as makeup brush handles, powder puff boxes, etc., after electroplating, are not only beautiful, but also easier to clean and maintain. In a survey on the user experience of makeup tools, 70% of users said that they are more willing to use makeup tools with electroplated appearance, believing that they have a higher sense of quality.
Summary: The surface electroplating process of cosmetic glass packaging plays a key role in improving product visual effects, durability and market competitiveness. From the advantages of electroplating, to the rich material selection, to the diverse coating types and rigorous process flow, each link is closely linked to create high-quality cosmetic packaging. As consumers’ requirements for cosmetic packaging continue to increase, the electroplating process will continue to innovate and develop, bringing more surprises and opportunities to the cosmetics industry. Whether it is the stunning appearance of the lipstick shell, or the quality upgrade of the bottle cap shell and makeup tool components, the electroplating process will continue to help cosmetics brands shine in the market.
If you have specific requirements for the data support, case selection, or chart presentation of certain arguments, please let me know and I can further optimize and improve them.
Explore the electroplating process for cosmetic glass packaging—its principles, advantages, materials, coatings, and applications for enhanced beauty and durability.
Explore the best bottles for storing essential oils. Learn about glass vs. plastic, color options, and tips for preserving oil potency.
Explore cosmetic glass bottles—safety, eco benefits, types, coloring, mold costs, MOQ, and production tips—in one expert, data-rich guide.
Explore custom vs. stock bottles for skincare packaging. Learn how Yafeng’s solutions boost brand identity, quality, and efficiency in this in-depth guide.
Discover the spray coating process for cosmetic glass packaging, including techniques, benefits, and tips to enhance product appeal and brand value.
Discover how spray coating enhances skincare and perfume packaging by improving appearance, brand identity, durability, and safety with advanced technology.
Explore custom vs. stock bottles for skincare packaging. Learn how Yafeng’s solutions boost brand identity, quality, and efficiency in this in-depth guide.
Discover how gradient color spray transforms cosmetic glass bottles, enhances brand image, and boosts product appeal with expert insights from Yafeng Packaging.
Discover how rattan aromatherapy works and why glass bottles are the best choice for long-lasting scent, safety, and sustainable, elegant packaging.
Discover the top 10 woods for perfume caps, comparing texture, pros, cons, and price to help you choose the best material for stylish, high-quality packaging.
Explore cosmetic glass bottles—safety, eco benefits, types, coloring, mold costs, MOQ, and production tips—in one expert, data-rich guide.
WhatsApp us