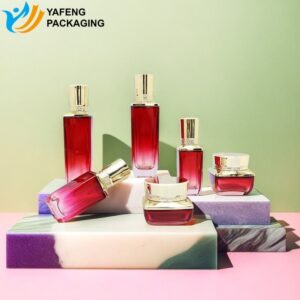
News & Blog
Great things in business are never done by one person. They’re done by a team of people. We have that dynamic group of peoples
In the field of beauty products, packaging is not just a container for products, it is closely linked to product quality and brand image. This article explores the significant advantages of amber glass bottles and jars in beauty product packaging, and elaborates on the key measures to ensure their quality and stability. From multiple dimensions such as material properties, protective functions, aesthetic value, and environmental protection characteristics, it provides a comprehensive and professional reference for beauty brands and consumers in packaging selection.
The preparation of amber glass requires several key steps. First, sand, soda ash, and limestone are fully mixed in a specific ratio, and then sent to a furnace and heated to about 1500โ. Under this high temperature environment, these raw materials gradually melt and form a uniform liquid. Next, molten iron, sulfur and carbon are added to the liquid glass, which fully blends with the liquid glass and gives the glass a unique amber color. After that, the liquid glass is processed into common shapes such as bottles and jars using precision equipment. As the temperature drops, the glass cools and solidifies, eventually becoming the amber glass products we see. According to industry data, with efficient furnace equipment and precise process control, the production efficiency of modern amber glass has increased by 30% compared with ten years ago, and the production cycle of a single product has been shortened from an average of 30 minutes to about 20 minutes. According to statistics from the International Glass Association, after adopting new furnace technology, the daily output of amber glass in some advanced companies has increased from 50 tons to 65 tons. If a flowchart of the amber glass production process can be attached here, it will help readers understand this production process more intuitively.
Sand, soda ash and limestone are the main basic raw materials for amber glass, and their quality directly determines the quality of the glass. High-quality sand should have uniform particles and extremely high purity. For example, the sand used to produce high-end amber glass packaging usually needs to have a silica content of more than 99%. According to industry research, the average silica purity of the sand used by the top domestic glass manufacturers has stabilized at around 99.5%, laying a solid foundation for high-quality glass production. There are also strict requirements for the purity and particle size of soda ash. High-purity soda ash can make the glass melt more evenly, and the appropriate particle size helps to accurately control the melting rate. Limestone must also be kept pure to prevent impurities that affect the performance of the glass.
Iron, sulfur and carbon are key colorants that give glass amber color, and accurate control of their addition is crucial. Slight deviations in proportion may lead to significant differences in glass color and affect the consistency of product appearance. Professional glass manufacturers use high-precision metering equipment to ensure that the amount of each colorant added is accurate to several decimal places. Taking mass production as an example, the error of iron addition in each batch of glass is controlled within ยฑ0.001% to ensure the stability of amber color.
In the selection of cosmetic packaging materials, amber glass is favored because of its chemical inertness. Glass is essentially a chemically neutral substance and will not react chemically with cosmetic formulas. According to research data from the American Society of Cosmetic Chemists, when using ordinary packaging materials, about 30% of products will have composition changes during the shelf life, while this proportion is only 5% for products packaged in amber glass.
Taking a high-end essence of Estee Lauder as an example, when the R&D personnel conducted stability tests, they placed the essence in ordinary plastic packaging and amber glass packaging respectively, and placed them in the same high temperature and high humidity environment. After several months, it was found that the active ingredient content of the essence in the plastic packaging decreased by about 20%, and the texture became thinner; while the active ingredient of the essence in the amber glass packaging only decreased by 3%, the texture remained stable, and it can continue to provide consumers with stable skin care effects. Since amber glass does not react with product formulas, it ensures that product ingredients are not affected by packaging, maintains product effectiveness and purity, and prevents harmful chemicals or toxins from penetrating from packaging into products, ensuring the safety of products for skin use.
In the glassmaking process, temperature control during the high-temperature melting stage is a key link. The melting temperature of around 1500ยฐC needs to be highly stable, and the fluctuation range is generally controlled within ยฑ10ยฐC. If the temperature is too high, the glass liquid may be over-oxidized, affecting its transparency and chemical stability; if the temperature is too low, the raw materials will not be fully melted, causing defects such as bubbles and stones inside the glass. Modern glass furnaces are equipped with advanced temperature control systems that can monitor and automatically adjust the temperature in real time to ensure the stability of the entire production process.
The molding process of shaping liquid glass into bottles, jars, etc. also has a significant impact on quality. The pressure, speed of the machine and the accuracy of the mold must be strictly controlled. Taking blow molding as an example, the blow molding pressure needs to be precisely adjusted according to the viscosity of the glass liquid and the shape of the product. Excessive pressure may cause uneven glass wall thickness, and too little pressure will not allow the glass to fully fit the mold, affecting the appearance and strength of the product. The surface finish and dimensional accuracy of the mold are also critical. High-precision molds can ensure consistent product shapes and effectively reduce the defective rate. For example, when the mold accuracy reaches ยฑ0.05mm, the product shape consistency can reach more than 98%, and the defective rate can be controlled within 5%. In the glass packaging production factory at the forefront of the industry, ultra-precision mold processing technology is used. The mold accuracy has reached ยฑ0.03mm, the product shape consistency has been increased to more than 99%, and the defective rate has been further reduced to less than 3%, greatly improving production efficiency and product quality. According to industry statistics, after the mold accuracy is increased from ยฑ0.05mm to ยฑ0.03mm, the production time of a single product can be shortened by about 5%, and the production efficiency is significantly improved.
Daily skin care products are mostly placed on shelves for easy access, which makes them very easy to be exposed to natural light. Blue light and ultraviolet rays in natural light will affect the product formula and reduce the product efficacy. According to statistics, about 60% of skin care products have an average shelf life shortened by 3 months due to light exposure.
SkinCeuticals Vitamin C Essence is a typical case. Vitamin C is chemically active and easily oxidized. When ordinary transparent glass packaging is used, it is easy to change color and become ineffective under light. After SkinCeuticals can choose amber glass packaging, it has been tested that under normal indoor light environment, the effective shelf life of the product can be extended to 12 months, which is 6 months longer than ordinary packaging. Consumers feedback that this essence packaged in amber glass has better stability and longer-lasting effect in daily storage. Therefore, product storage instructions usually warn to avoid direct sunlight, while amber glass can absorb harmful light wavelengths, provide protection for the product, and reduce product loss caused by light. The comparison of the effect of different packaging on the product’s exposure to light is as follows:
Packaging type | Changes in effective shelf life after exposure to light | Changes in product efficacy |
---|---|---|
Ordinary transparent glass packaging | An average of 3 months shorter | Efficacy is significantly reduced, such as vitamin C essence is easy to change color and become ineffective, and the antioxidant activity is reduced by about 50% |
Amber glass packaging | Extended to 12 months (6 months longer than ordinary packaging) | Stable efficacy, can maintain the original effect of the product, and the antioxidant activity remains above 95% |
ย | ย |
Every amber glass packaged product must undergo strict appearance inspection before leaving the factory. The product is checked for defects such as bubbles, scratches, and deformations by combining manual visual inspection with automated optical inspection equipment. During manual inspection, inspectors need to observe the product in all directions under specific lighting conditions and in accordance with standard procedures. Automated optical inspection equipment uses high-definition cameras and image recognition technology to quickly and accurately detect subtle appearance defects with an accuracy of up to 0.1 mm.
In addition to appearance testing, performance testing of glass packaging is also essential. For example, the ability of a product to withstand pressure during transportation and storage is evaluated through compression testing. Generally, amber glass bottles are required to withstand a certain weight of static pressure without breaking. The chemical stability of glass is tested by soaking glass samples in specific chemical solutions to observe whether any components are dissolved to ensure that they will not react with the cosmetic formula. The gas and moisture barrier performance test simulates the actual environment through professional equipment to test the barrier effect of glass on oxygen, water vapor, etc. to ensure the shelf life of the product.
In addition to its excellent light-proof performance, amber glass performs well in blocking gases, moisture and other environmental factors that affect the quality of cosmetics. For moisturizing creams, moisture retention is crucial to its effectiveness. If the packaging cannot effectively prevent water loss, the cream will dry out and lose its moisturizing effect.
Lancome Absolu Facial Cream is packaged in amber glass jars. Experimental data show that after being placed in the same environment for 6 months, the moisture loss rate of ordinary plastic-packaged creams is 15%, while the moisture loss rate of amber glass-packaged creams is only 5%. At the same time, it can effectively prevent external dust, microorganisms and other pollutants from entering the product. Related studies have shown that the microbial contamination rate of eye serums packaged in amber glass is 80% lower than that of ordinary packaging, which greatly reduces the risk of product deterioration and ensures product safety and effectiveness. This barrier protection is particularly critical for cosmetics used around the eyes or other sensitive parts of the face. For example, La Mer eye serum is packaged in amber glass, providing safer and more stable product protection for eye skin and reducing the risk of eye discomfort caused by product contamination. The data on the impact of different packaging on product moisture retention and microbial contamination are as follows:
Packaging type | 6-month moisture loss rate | Microbial contamination rate |
---|---|---|
Ordinary plastic packaging | 15% | Higher, about 10% |
Amber glass packaging | 5% | 80% lower than ordinary packaging, about 2% |
ย | ย |
Design appropriate glass packaging structure and thickness according to the characteristics of different beauty products, such as pH, volatility, etc. For products with strong acidity, it may be necessary to increase the glass thickness or use special coating treatment to enhance its corrosion resistance. For volatile products, ensure that the bottle cap is well sealed, use special sealing structure and materials to reduce product volatilization losses. For example, for acidic products with a pH value of 3-4, the glass thickness needs to be increased by 0.5mm, and an acid-resistant coating is used to effectively prevent the glass from being corroded. After testing, in a simulated acidic environment, untreated glass packaging showed obvious signs of corrosion within 1 month, while glass packaging treated with increased thickness and acid-resistant coating showed no obvious corrosion within 6 months.
During product transportation and storage, reasonable protective design can effectively prevent glass packaging from being damaged. Customized cushioning packaging materials, such as foam and air cushions, are used to tightly wrap glass packaging products to reduce damage caused by vibration and collision. When packing products, reasonable layout is planned to avoid mutual squeezing between products, further improving stability during transportation. After actual testing, after using customized cushioning packaging, the breakage rate of glass packaging products during transportation can be reduced to 3%. According to logistics industry statistics, after adopting professional protective packaging solutions, the breakage rate of glass packaging products in long-distance transportation has been reduced from the original 10% to less than 3%, greatly reducing product loss costs. In the scenario of long-distance transportation (more than 1,000 kilometers), when customized protective packaging is not used, the number of broken products per 1,000 pieces is about 100 pieces, and the number of broken products is reduced to less than 30 pieces after using it.
With its warm golden hue and unique light refraction effect, amber glass shows a unique beauty. This appearance is easily reminiscent of old-fashioned medicine bottles and perfumes, triggering consumers’ associations with luxury. Market research shows that about 70% of consumers believe that products packaged in amber glass are more high-end and are willing to pay an average of 20% higher prices for such products. Especially for natural or organic cosmetics, amber matches the natural and earthy tones of the product and can better highlight the natural attributes of the product.
Some of L’Occitane’s herbal skin care products are packaged in amber glass, which not only shows the natural ingredients of the product, but also enhances the overall texture. The weight and smooth texture of the glass itself further increase the perceived value of the product. For example, Jo Malone Aromatherapy Essential Oil is packaged in amber glass bottles, which not only visually presents a sense of high quality, but also allows consumers to feel the luxury of the product in their hands. Brands can choose amber glass packaging to increase the added value of their products, which may lead to higher prices.
Amber glass is a packaging material with a wide range of applicability. It can be used for packaging a variety of beauty products, such as moisturizers and essences, and can effectively protect the active ingredients in them; for essential oils that are easily oxidized and deteriorated, amber glass is an ideal choice. According to statistics, the shelf life of essential oils packaged in amber glass can be extended by 2 to 3 years compared to ordinary packaging.times. Taking some of doTERRA’s essential oil products as an example, the shelf life of ordinary packaging is 1 year, which can be extended to 3 years after amber glass packaging, ensuring that the essential oils are still fragrant and effective after long-term storage.
In addition, amber glass is also suitable for cosmetics, lip balm and other products. For example, some Yves Saint Laurent lipstick products use amber glass tubes, which not only ensure product quality but also add a sense of fashion. Whether it is a paste, liquid or solid beauty product, amber glass can meet different packaging needs.
In summary, amber glass bottles and glass jars have many significant advantages in the field of beauty product packaging. It can ensure the stability of product ingredients, effectively resist light and environmental damage, give products a retro and luxurious aesthetic charm, and is suitable for all kinds of beauty product packaging, and is in line with environmental protection concepts. Although glass has the problems of fragility and high transportation costs, these problems can be properly solved through a series of measures from raw material control, production process specifications, quality inspection improvement to packaging design optimization. For beauty brands that pursue high quality, high value and pay attention to the environment, amber glass is undoubtedly the preferred packaging material, which will effectively help brands stand out in the fiercely competitive market.
At Yafeng Packaging, we offer a wide range of amber packaging options. They can be easily customized with labels and branding, and can be made into a variety of shapes and sizes to suit different product needs. If you would like to discuss your packaging requirements, please contact a member of our sales team.
Elevate your beauty brand with strategic packaging design! Explore luxury & sustainable cosmetic packaging trends, brand collaborations & unboxing experiences.
Elevate your cosmetic brand with standout packaging! Learn how to customize designs, choose colors, leverage trends, and create an unforgettable unboxing experience.
Discover the secrets to preserving perfume: how bottle design and temperature control impact fragrance quality. Learn expert tips for optimal storage.
Discover the elegance and sustainability of glass packaging for cosmetics! Learn how glass bottles protect skincare and align with eco-friendly solutions.
Explore the evolving cosmetic packaging market! Learn about rising material costs, design trends, eco-friendly solutions, and strategies for beauty brands to thrive.
Amber glass bottles offer luxury, UV protection, and stability for beauty packaging. Learn about their production, quality control, and benefits for skincare brands.
Single-material all-plastic pumps are revolutionizing cosmetic packaging with eco-friendly, cost-effective, and recyclable designs, driving sustainability and brand appeal.
Discover 10 expert tips to choose the best cosmetic bottles, ensuring quality, durability, and sustainability while enhancing your beauty routine effortlessly.
Glass bottles are the best for hair oil storage due to their non-reactivity, UV protection, and ability to preserve quality, ensuring longer shelf life and better efficacy.
Explore the essential role of spray pumps in cosmetics, covering molding, surface treatment, components, and atomization. Learn how spray pumps enhance product performance and user experience in perfumes, gels, and more.
Discover the secrets to preserving perfume: how bottle design and temperature control impact fragrance quality. Learn expert tips for optimal storage.
WhatsApp us