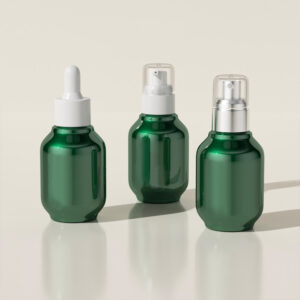
Haberler & Blog
İş dünyasında büyük işler asla tek bir kişi tarafından yapılmaz. Bunlar bir ekip tarafından yapılıyor. Bizde bu dinamik insan grubu var.
Kozmetik cam losyon şişeleri dolum sırasında sıklıkla çatlamakta, bu da sadece ürün kaybına neden olmakla kalmayıp aynı zamanda ürün kalitesi ve güvenliği için de bir tehdit oluşturmaktadır. Bu makale, iç basınç ve dış basınç gibi birden fazla faktörü kapsayan bu sorunun çeşitli nedenlerini kapsamlı ve derinlemesine araştırmakta ve gerçek vakalar ve veri desteği aracılığıyla her bir faktörün etki mekanizmasını detaylandırmaktadır. Aynı zamanda, kozmetik üreticilerinin şişe ağzı çatlaması vakalarını etkili bir şekilde azaltmalarına ve üretim verimliliğini ve ürün kalitesini artırmalarına yardımcı olmak için bir dizi hedefli çözüm önerilmektedir.
Kozmetik üretimi alanında, cam losyon şişeleri iyi stabilite, estetik ve çevre koruma özellikleri nedeniyle birçok marka için tercih edilen ambalaj kabı haline gelmiştir. Bununla birlikte, dolum sürecinde cam losyon şişelerinin çatlaması yaygındır ve bu da işletmelere birçok sıkıntı getirir. Bu sorunu çözmek, ürün kalitesini artırmak, üretim maliyetlerini düşürmek ve tüketici haklarını korumak için çok önemlidir. Şimdi, şişe ağzı yırtılmasının nedenlerine daha yakından bakalım.
Gaz içeren sıvılarla (gazlı içecekler veya bira vb.) doldurulan cam şişeler için iç basınç dolum ve sonraki taşıma sırasında artmaya devam edecektir. Örneğin, gazlı içecekler doldurulduktan sonra karbondioksit çözünmeye ve basınç oluşturmaya devam edecektir. Şişenin içindeki basınç cam şişenin dayanabileceği sınırı aştığında, şişe kırılma riski taşır. Buna ek olarak, bazı sıcak dolgulu veya yüksek sıcaklıkta sterilize edilmiş kozmetik emülsiyonlar, ısıtma işlemi sırasında, termal genleşme ve büzülme prensibi nedeniyle, emülsiyonun hacmi genişler ve bu da iç basıncın artmasına neden olur. İlgili çalışmalar, iç basınç cam şişenin dayanmak üzere tasarlandığı basıncın 1,5 katına ulaştığında, yırtılma olasılığının önemli ölçüde artarak 80%'den daha fazla olacağını göstermiştir.
Cam darboğaz malzemesi yetersiz ve conta çok ince olduğunda, dolum ekipmanının pompa kafası çalışma sırasında cam omzuna çarpabilir. Özellikle dolum tamamlandıktan sonra, makine pompa kafasını sıktığında, darboğaz üzerinde ek gerilim uygulayarak darboğazın kırılmasına neden olur. Üretim hattından alınan geri bildirimlere göre, yetersiz darboğaz malzemesine ve ince contalara sahip cam şişeler kullanıldığında, dış basıncın neden olduğu şişe ağzı yırtılması sorunu bazı partilerde 30% kadar yüksektir.
Yüksek sıcaklıkta sterilizasyondan sonraki soğutma aşamasında, cam şişe ciddi bir yüksek ve düşük sıcaklık şoku yaşar. Cam şişe malzemesinin düzensizliği nedeniyle, her bir parçanın termal genleşme ve büzülme derecesi farklıdır, dolayısıyla iç gerilim oluşturur. Bu iç gerilim cam şişenin taşıma sınırını aştığında, kırılmaya neden olacaktır. Örnek olarak bir kozmetik şirketini ele alalım. Soğutma süreci optimize edilmeden önce, termal şokun neden olduğu şişe ağzı yırtılması toplam yırtılmaların yaklaşık 25%'sini oluşturuyordu.
Cam şişelerde termal stres ve yapısal stres vardır. Termal stres, cam şişelerin üretimi sırasında ikincil tavlama işlemi ile etkili bir şekilde ortadan kaldırılabilir. Ancak yapısal stres tavlama işlemi sırasında ortadan kaldırılamaz ve cam üründe kalıcı olarak kalır. Yapısal gerilim cam ürünün kendi mekanik mukavemetini aştığında, ürün kırılacaktır. Araştırma verileri, aşırı yapısal strese sahip cam şişelerin kırılma riskinin normal şişelere göre 5 kat daha fazla olduğunu göstermektedir.
Cam şişe tipi | Kırılma olasılığı | İç gerilim (optik yol farkı) | Şişe duvar kalınlığı homojenliği | Termal kararlılık |
---|---|---|---|---|
Normal cam şişe | Yaklaşık 0,5% | ≤40nm/cm | Daha iyi, şişe duvar kalınlığı sapması ±0,2 mm dahilindedir | Yaklaşık 120 ℃ sıcaklık farkına dayanabilir |
Aşırı yapısal gerilime sahip cam şişe | 20% Hakkında | ≥80nm/cm | Zayıf, şişe duvar kalınlığı sapması ±0,5 mm'ye ulaşabilir | Sadece yaklaşık 80°C'lik bir sıcaklık farkına dayanabilir |
Cam şişenin alt yüzeyi ile şişe ağzının merkez çizgisi arasındaki dikeylik, dikey eksen sapmasıdır. Cam şişenin dikeyliği iyi değilse, doldurma ve kapatma işlemleri sırasında pozisyon sapması meydana gelme olasılığı çok yüksektir ve bu da cam şişenin ezilmesine yol açacaktır. Gerçek üretimde, dolum ve kapatma sırasında dikey eksen sapması standart değer olan 0,5 mm'yi aşan cam şişelerin kırılma oranı 15%'ye ulaşabilir.
Cam şişelerin duvar kalınlığının ve taban kalınlığının homojenliği, anizotropi derecesini doğrudan belirler ve iç basınca ve termal şoka karşı direnci etkileyen temel faktörlerden biridir. Düzensiz duvar kalınlığına sahip cam şişeler, iç basınca veya sıcaklık değişimlerine maruz kaldıklarında ilk olarak zayıf kısımlardan kırılmaya eğilimlidir. Farklı et kalınlığı homojenliğine sahip cam şişeler üzerinde yapılan deneysel testler sonucunda, zayıf et kalınlığı homojenliğine sahip şişelerin iç basınç direncinin, iyi homojenliğe sahip şişelere göre yaklaşık 30% daha düşük olduğu bulunmuştur.
Doldurma ve taşıma işlemi sırasında cam şişeler birbirleriyle çarpışacaktır. Bu mekanik darbe, cam şişelerin mukavemeti için büyük bir testtir. Darbe direnci zayıf olan cam şişeler, sık darbe altında şişe ağzında ve şişe gövdesinde çatlamaya ve hatta kırılmaya eğilimlidir. Örneğin, uzun mesafeli nakliye sırasında, yeterli tamponlama önlemleri alınmayan cam şişeler, yetersiz darbe direnci nedeniyle 10% - 20% kırılma oranına sahip olabilir.
Çevre bilincinin artmasıyla birlikte geri dönüştürülmüş cam şişe miktarı her geçen yıl artmıştır. Ancak, geri dönüştürülmüş cam şişelerin performansı genellikle yeni şişelere göre daha düşüktür. Bir kozmetik markası tarafından kullanılan geri dönüştürülmüş şişelerin verileri örnek olarak alındığında, geri dönüştürülmüş şişelerin kırılma oranı yeni şişelere göre yaklaşık 40% daha yüksektir. Bunun temel nedeni, geri dönüştürülmüş şişelerin yapısının ve performansının tekrarlanan kullanım, temizlik ve nakliye sırasında değişen derecelerde zarar görmesidir.
Dolum işlemi sırasında basınca dayanacak kadar güçlü olmasını sağlamak için cam şişenin ağız ve gövde yapısını yeniden tasarlayın. Sonlu elemanlar analizi gibi teknik araçlarla, yapısal stabiliteyi artırmak için cam şişenin şeklini ve kalınlık dağılımını optimize edin. Örneğin, şişe ağzının kalınlığını 1 mm artırmak, şişe ağzının basınç dayanımını 20% artırabilir.
Sıcaklık stresinin neden olduğu yırtılmayı azaltmak için emülsiyonun dolum sıcaklığını cam şişenin termal genleşme katsayısı ile eşleştirecek şekilde hassas bir şekilde kontrol edin. Doldurmadan önce, emülsiyon sıcaklığını uygun bir aralıkta stabilize etmek için bir sıcaklık kontrol sistemi kullanın. Pratik deneyimlere göre, dolum sıcaklığının 25℃ - 30℃'de kontrol edilmesi, sıcaklık sorunlarının neden olduğu şişe ağzı yırtılması riskini etkili bir şekilde azaltabilir.
Emülsiyonun şişe ağzına çok hızlı veya çok şiddetli bir şekilde çarpmasını önlemek için nazik ve düzgün bir doldurma yöntemi kullanın. Doldurma ekipmanının parametrelerini ayarlayarak, emülsiyonun şişeye eşit şekilde akmasını sağlamak için doldurma hızını ve basıncını kontrol edin. Gerçek üretim, doldurma hızının 20% azaltılmasının, doldurma darbesinin neden olduğu şişe ağzı yırtılmasını 50% azaltabileceğini göstermektedir.
Şişe kapağı ve şişe ağzı boyutunun doğru bir şekilde eşleştiğinden, sızdırmazlığın iyi olduğundan ve basıncın eşit olarak dağıtılabildiğinden emin olun. Şişe kapağının malzemesini ve yapısını tarayın ve şişe kapağını yapmak için yüksek kaliteli malzemeler kullanın. Örneğin, belirli bir esneklik ve tokluğa sahip plastik şişe kapaklarının kullanılması, sıkma sırasında şişe ağzı üzerindeki basıncı etkili bir şekilde tamponlayabilir.
Dolumdan önce, cam şişeler üzerinde kapsamlı kalite denetimi yapmak için yüksek hassasiyetli denetim ekipmanı kullanın, örneğin şişe gövdesinde ve şişe ağzında kusur ve çatlak olup olmadığını kontrol etmek için optik denetim ekipmanı kullanmak gibi. Sıkı tarama sayesinde, niteliksiz cam şişeler elenerek dolum sürecine girmeleri engellenir. Veriler, sıkı kalite denetiminden sonra, cam şişe kalite sorunlarından kaynaklanan şişe ağzı yırtılmasının 80%'den daha fazla azaltılabileceğini göstermektedir.
Dolum operatörlerinin çalışma becerilerini ve kalite farkındalıklarını geliştirmek için sistematik eğitimler gerçekleştirin. Eğitim içeriği, doğru ekipman çalıştırma prosedürlerini, dolum tekniklerini ve yaygın sorun ele alma yöntemlerini içerir. Eğitimden sonra, insan faktörlerinden kaynaklanan şişe ağzı hasarı önemli ölçüde azaltılmış ve üretim verimliliği de artırılmıştır.
Doldurduktan sonra, cam şişeleri korumak için köpük pedler, balonlu filmler ve diğer yastıklama malzemeleri gibi uygun ambalaj malzemeleri kullanın. Nakliye sırasında, darbeleri ve titreşimleri azaltmak için nakliye rotasını makul bir şekilde planlayın. Uygulama, mükemmel paketleme ve nakliye koruma önlemleri alındıktan sonra, nakliye bağlantısındaki cam şişelerin kırılma oranının 5% içinde kontrol edilebileceğini kanıtlamıştır.
Doldurma işlemi sırasında kozmetik cam emülsiyon şişesinin ağzının yırtılması sorunu, iç basınç, dış basınç, termal şok, iç gerilim, dikey eksen sapması, duvar kalınlığı, darbe direnci ve geri dönüştürülmüş şişeler gibi çok sayıda faktörün birleşik etkisinin sonucudur. Şişe tasarımını optimize ederek, dolum sıcaklığını kontrol ederek, dolum sürecini iyileştirerek, uygun bir şişe kapağı seçerek, kalite denetimini güçlendirerek, operatörleri eğiterek ve iyi bir paketleme ve nakliye koruması yaparak, şişe ağzı yırtılması insidansı önemli ölçüde azaltılabilir ve ürün kalitesi ve üretim verimliliği artırılabilir. Her kozmetik üreticisi, şişe ağzı yırtılması sorunuyla etkili bir şekilde başa çıkmak ve üretimin sorunsuz ilerlemesini sağlamak için bu çözümleri gerçek üretim ortamına ve koşullarına göre esnek bir şekilde ayarlamalı ve optimize etmelidir.
Şık ve yüksek kaliteli ambalajlar için en iyi malzemeyi seçmenize yardımcı olmak üzere doku, artılar, eksiler ve fiyatı karşılaştırarak parfüm kapakları için en iyi 10 ahşabı keşfedin.
Gelişen uçucu yağ pazarını keşfedin! Büyüme etkenlerini, trendleri, kozmetik ve kişisel bakımdaki kullanımları ve sürekli genişleme tahminlerini keşfedin.
Cam şişelerin nasıl yapıldığını keşfedin! Hammaddeden şekillendirmeye ve tavlamaya kadar, bu günlük kabın büyüleyici üretim sürecini keşfedin.
Cilt bakımı ambalajları için özel ve stok şişeleri keşfedin. Bu derinlemesine kılavuzda Yafeng'in çözümlerinin marka kimliğini, kaliteyi ve verimliliği nasıl artırdığını öğrenin.
Püskürtme pompaları hakkında bilgi edinin: türleri, kullanımları ve ihtiyaçlarınız için en iyisini nasıl seçeceğiniz.
Sprey kaplamanın, ileri teknoloji ile görünümü, marka kimliğini, dayanıklılığı ve güvenliği iyileştirerek cilt bakımı ve parfüm ambalajlarını nasıl geliştirdiğini keşfedin.
Cilt bakımı ambalajları için özel ve stok şişeleri keşfedin. Bu derinlemesine kılavuzda Yafeng'in çözümlerinin marka kimliğini, kaliteyi ve verimliliği nasıl artırdığını öğrenin.
Degrade renk spreyinin kozmetik cam şişelerini nasıl dönüştürdüğünü, marka imajını nasıl geliştirdiğini ve ürün çekiciliğini nasıl artırdığını Yafeng Packaging'in uzman görüşleriyle keşfedin.
Rattan aromaterapinin nasıl çalıştığını ve cam şişelerin neden uzun süre kalıcı koku, güvenlik ve sürdürülebilir, zarif ambalaj için en iyi seçim olduğunu keşfedin.
Şık ve yüksek kaliteli ambalajlar için en iyi malzemeyi seçmenize yardımcı olmak üzere doku, artılar, eksiler ve fiyatı karşılaştırarak parfüm kapakları için en iyi 10 ahşabı keşfedin.
Kozmetik cam şişelerin güvenliğini, ekolojik faydalarını, türlerini, renklendirmesini, kalıp maliyetlerini, MOQ'unu ve üretim ipuçlarını tek bir uzman, veri açısından zengin kılavuzda keşfedin.
Bize WhatsApp