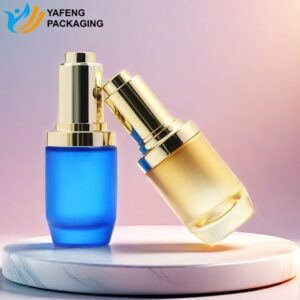
Nachrichten & Blog
Großartige Leistungen in der Wirtschaft werden nie von einer einzelnen Person erbracht. Sie werden von einem Team von Menschen vollbracht. Wir haben diese dynamische Gruppe von Menschen
Spray pumps are key supporting products for cosmetic containers and are widely used in water-based and essence products such as perfumes, gel water, and air fresheners. Their performance directly affects user experience. This article deeply analyzes the basic knowledge of spray pumps, including molding process, surface treatment, graphic processing, main accessories, product structure, water outlet and atomization principle, application scenarios, and specification parameters. Through rich data, tables, and illustrations, this article comprehensively presents the secrets of spray pump products to you, helping you to gain a deeper understanding of this crucial packaging material category in the cosmetics industry.
The molding process of the spray pump involves the use of a variety of materials and technologies. Although the bayonet (semi-bayonet aluminum, full-bayonet aluminum) and screw-on parts may look metallic, they are actually made of plastic. Some products will cover the plastic with an aluminum cover or electroplated aluminum to enhance the appearance and protective performance.
Most of the internal parts of the spray pump, such as the pump body and nozzle, are made of plastic materials such as PE (polyethylene), PP (polypropylene), and LDPE (low-density polyethylene), and are manufactured through injection molding. Injection molding is efficient and precise, and can mass-produce accessories with complex shapes and uniform specifications. According to statistics, among spray pump manufacturers, about 80% of the internal parts are injection molded.
However, accessories such as glass beads and springs are usually purchased by professional parts suppliers due to their special materials and manufacturing process requirements. For example, glass beads need to have high-precision dimensions and good wear resistance, and professional glass product manufacturers can better meet this demand; springs require specific elastic coefficients and durability, and professional spring manufacturers can ensure the stability of product quality.
The main components of the spray pump can be treated in a variety of ways to meet different appearance and performance requirements.
Vacuum plating: By depositing metal ions on the surface of the component under a vacuum environment, a uniform, bright and metallic coating can be formed. Vacuum plating can enhance the aesthetics of the spray pump and make it more upscale. For example, on some high-end perfume spray pumps, the vacuum-plated metal layer can reflect a dazzling luster and enhance the visual appeal of the product. According to market research, about 30% of high-end cosmetic spray pumps use vacuum plating technology.
Anodized aluminum: Anodized aluminum is a commonly used surface decoration material. It can be transferred to the surface of the spray pump component by hot pressing and other methods to present a rich color and pattern effect. Anodized aluminum has good wear resistance and corrosion resistance, which can effectively protect the surface of the component and add a unique decorative style to the product. In the spray pump design of some fashion brands, the use of anodized aluminum can achieve a unique brand logo and personalized pattern, and enhance product recognition.
Spraying: The paint is evenly sprayed on the surface of the component through a spray gun and other equipment to form a protective film. The spraying process can choose paints of different colors and textures to achieve a variety of appearance effects. For example, matte spraying can make the spray pump present a low-key and soft texture, which is suitable for products pursuing a simple style; while glossy spraying can enhance the gloss of the product and make it more visually impactful. About 40% of conventional cosmetic spray pumps are surface treated by spraying.
Injection color: Add color masterbatch of specific color to the plastic raw material, and directly give the component the required color through injection molding. This method is relatively low-cost, and the color is uniform and stable. For some products that have specific requirements for appearance color and focus on cost control, injection color is a common choice.
The nozzle surface and the braces surface of the spray pump are feasible for graphic printing. Common processes include hot stamping and silk screen printing.
Heißprägen: Use high temperature and high pressure to transfer metal foil to the surface of the product to form gold or other metallic colors. Hot stamping can make the graphics present a noble and gorgeous texture, and enhance the overall grade of the product. For example, on the nozzles of some high-end perfume spray pumps, the hot stamping process can print brand logos or exquisite patterns to highlight the brand’s luxury positioning.
Silk screen printing: Through screen printing technology, ink is printed on the surface of the product through the screen, which can achieve the printing of multiple colors and complex patterns. The cost of the silk screen printing process is relatively low, and it is highly flexible and suitable for production needs of different batches. On some popular cosmetic spray pumps, silk screen printing can print product names, instructions for use and other information for the convenience of consumers.
However, in order to maintain the simplicity and beauty of the product appearance, and at the same time avoid the possible impact of printed graphics on the spray effect, generally less printing is performed on the nozzle. According to industry observations, about 85% of the spray pump nozzles remain plain.
Conventional spray pumps are composed of multiple key accessories, each of which plays a unique role in the entire system.
Nose/Head: The part that the user directly operates, generates power by pressing, and drives the internal components to work. The design of the nozzle should take ergonomics into consideration to ensure that the user presses comfortably and labor-savingly. Different brands and types of spray pumps have different shapes and sizes of nozzles to suit different user groups and product positioning.
Diffuser nozzle: Responsible for dispersing the liquid sprayed from the pump body so that it can be sprayed more evenly on the target surface. The structural design of the diffuser nozzle will affect the coverage and particle size of the spray. For example, in a perfume spray pump, the diffuser nozzle is usually designed to form a fine mist of liquid to evenly adhere to the skin; while in an air freshener spray pump, the diffuser nozzle may make the spray coverage wider to quickly diffuse the fragrance.
Center duct: Connects the pump body and the nozzle, guides the liquid from the pump body to the nozzle, and plays a supporting and positioning role during the pressing process. The material and inner diameter of the center duct will affect the flow rate of the liquid and the spray effect. Generally, plastic material is used, and its inner diameter is designed according to the water output requirements of the product.
Lock cap: Used to fix the nozzle to prevent accidental pressing during transportation or storage, and at the same time protect the internal components. The design of the lock cap usually has a certain opening and closing resistance to ensure its stability. Some spray pump lock caps also have a special anti-slip design for easy user operation.
Gasket: Installed between the pump body and the container bottle mouth, it plays a sealing role to prevent liquid leakage. The material of the gasket is mostly rubber or silicone, with good elasticity and sealing, and can adapt to the shape and size of different bottle mouths.
Piston core, piston: The piston and the piston seat cooperate to realize the suction and discharge functions inside the pump body. The piston is an open piston. When the compression rod moves upward, the pump body is open to the outside, the studio is closed, and the liquid is sucked in; when the compression rod moves downward, the volume of the studio is compressed and the liquid is squeezed out. The material and sealing performance of the piston directly affect the working efficiency and stability of the spray pump.
Spring: Provides reset power. After the pressing is completed, it pushes the piston seat and the piston upward to restore the pump body to its initial state and prepare for the next suction. The elastic coefficient of the spring needs to be selected according to the overall design of the spray pump to ensure a suitable pressing feel and reset speed.
Pump body: As the core component of the spray pump, it accommodates other accessories and realizes the suction and discharge of liquid through changes in the internal structure. The material and structural design of the pump body determine the durability and working performance of the spray pump.
Straw: Used to suck liquid from the bottom of the container and deliver it to the pump body. The length of the straw can be adjusted according to the height of the bottle to ensure that the liquid in the container can be fully sucked.
The product structure design of the spray pump needs to take into account a variety of factors to achieve efficient and stable spraying function. Different types of spray pumps have certain differences in structure, but generally follow similar design principles. The optimization goals of its structural design include improving liquid absorption efficiency, enhancing the uniformity and stability of the spray, reducing production costs, and improving product durability. For example, some new spray pumps adopt a more compact structural design, reducing the number of parts, which not only reduces the production and assembly costs, but also improves the overall reliability of the product. Through the structural analysis of different brands of spray pumps on the market, it is found that about 60% of the spray pumps have made different degrees of optimization and innovation in structural design.
Exhaust process: Assume that there is no liquid in the base working chamber in the initial state. When the pressing head is pressed, the compression rod drives the piston to move downward, the piston pushes the piston seat downward, the spring is compressed, the volume in the working chamber is compressed accordingly, and the air pressure increases. At this time, the water stop valve seals the upper port of the water pipe to prevent external air from entering. Since the piston and the piston seat are not completely closed, when the air pressure increases to a certain extent, the gas squeezes the gap between the piston and the piston seat, separating them, allowing the gas to escape, thus completing the exhaust process.
Water absorption process: After exhausting, release the pressing head, and the compressed spring releases the elastic potential energy to push the piston seat upward. During the upward movement of the piston seat, the gap between the piston seat and the piston gradually closes, and drives the piston and the compression rod to move upward together. At this time, the volume in the studio increases, the air pressure decreases, and it is close to a vacuum state. The air pressure above the liquid surface in the container is relatively large. Under the action of the air pressure difference, the liquid is pressed into the pump body to complete the water absorption process.
Water discharge process: Its principle is similar to the exhaust process, but the pump body is full of liquid at this time. When the pressing head is pressed again, on the one hand, the water stop valve seals the upper end of the water suction pipe to prevent the liquid from flowing back from the water suction pipe into the container; on the other hand, due to the extrusion of the liquid (incompressible fluid), the liquid will break the gap between the piston and the piston seat, flow into the compression pipe, and finally spray out from the nozzle.
In order to understand the water discharge principle more intuitively, the following table compares the state changes of each component in the three processes of exhaust, water absorption and water discharge:
Prozess | Press head state | Spring state | Piston position | Piston seat and piston gap | Water stop valve state | Liquid flow |
---|---|---|---|---|---|---|
Exhaust process | Press | Compress | Move down | Open | Close | No liquid flow, gas discharge |
Water absorption process | Release | Stretch | Move up | Close | Open | Liquid is sucked into the pump body from the container |
Water discharge process | Press | Compress | Move down | Open | Close | Liquid is sprayed from the pump body through the compression pipe and out of the nozzle |
When the liquid flows out of the nozzle, since the nozzle opening is very small, if the pressure is smooth, the liquid has a certain flow rate in the compression tube, and the liquid flow rate is very large at this time. This means that the air has a very large flow rate relative to the liquid, similar to the situation where a high-speed airflow impacts water droplets. The air impacts large water droplets into small water droplets, and after step-by-step refinement, the water droplets become smaller. At the same time, the high-speed flowing liquid will also drive the gas flow near the nozzle opening, making the speed of the gas near the nozzle opening larger. According to Bernoulli’s principle, the pressure decreases as the gas flow rate increases, thus forming a local negative pressure area. The surrounding air is mixed into the liquid under the action of the air pressure difference to form a gas-liquid mixture, which eventually causes the liquid to produce an atomization effect. Different types of spray pumps are basically the same in the atomization principle, but they will differ in the specific nozzle design and internal structure optimization to achieve a more delicate and uniform atomization effect. For example, some high-end perfume sprays Through the special design of the nozzle, the spray pump can make the droplet diameter reach 5-10 microns, while the droplet diameter of the ordinary spray pump may be between 20-50 microns.
Dispenser type: The dispenser of the cosmetic spray pump is divided into two types: tie-mouth type and screw-mouth type. The tie-mouth dispenser achieves sealing and connection by tightly tying the pump body and the bottle mouth. The installation is relatively simple, but the disassembly may be more troublesome; the screw-mouth dispenser is connected by thread, has better sealing and stability, and is easy to install and disassemble, suitable for different types of cosmetic packaging. In the market, about 70% of cosmetic spray pumps use screw-mouth dispensers.
Pump head specifications: The size of the pump head must be compatible with the caliber of the matching bottle body, and the specifications of the spray are generally between 12.5mm-24mm. The water output is usually 0.1ml/time-0.2ml/time, and the specific value depends on the product type and design requirements. For example, perfume spray pumps usually have a small water output to achieve a precise and delicate spraying effect; while gel water spray pumps may have a relatively large water output to meet the needs of large-area application. The length of the pipe with the same diameter can be customized according to the height of the bottle to ensure that the straw can fully absorb the liquid in the bottle.
Spray head metering: There are two main methods for measuring the dosage of liquid sprayed out by the spray head at one time: peeling measurement method and absolute value measurement method. The measurement error is usually controlled within 0.02g to ensure the accuracy of the product dosage. In addition, the metering can also be distinguished by the size of the pump body. The structural design of pump bodies of different sizes will affect the amount of liquid absorbed and sprayed each time it is pressed.
Mold situation: Due to the wide variety of spray pumps, including different specifications, structures and functional designs, a large number of different molds are required for production. The development and manufacturing costs of molds are high, which to a certain extent increases the production cost of spray pumps. It is understood that the development cost of a set of ordinary spray pump molds may range from tens of thousands to hundreds of thousands of yuan, while the cost of some specially designed molds is as high as millions of yuan.
As an indispensable packaging material in the cosmetics industry, spray pumps contain a wealth of knowledge and technical points in terms of molding process, surface treatment, graphic processing, accessory composition, product structure, water outlet and atomization principle, and application specifications in cosmetics. From the coordination of injection molding and external procurement in the molding process to the diverse choices of surface treatment to meet different aesthetic and functional requirements; from the unique functions of the main accessories to the complex and delicate physical processes behind the water outlet and atomization principles; from the adaptation of the dispenser type and the pump head specifications to the precise control of the nozzle metering and the consideration of the mold cost, each link is closely linked and jointly determines the performance and quality of the spray pump. A deep understanding of these basic knowledge will not only help cosmetics manufacturers choose suitable spray pump products, improve product quality and user experience, but also enable consumers to better understand the working principle and value of the cosmetic spray pump in their hands. In the future, with the continuous advancement and innovation of technology, spray pump products are expected to make greater breakthroughs in performance improvement, cost control and environmental protection, and continue to inject new vitality into the development of the cosmetics industry.
Entschlüsseln Sie die Geheimnisse der Parfümflaschengrößen! Dieser ultimative Leitfaden hilft Ihnen bei der Auswahl der perfekten Größe für Ihre Bedürfnisse, von reisefreundlichen 1,7 oz bis hin zu lang anhaltenden 3,4 oz.
Entschlüsseln Sie die Geheimnisse des Großhandels mit Parfüm und Flakons! Finden Sie Ihren perfekten Duft, entdecken Sie individuelle Flaschendesigns und beziehen Sie von Top-Lieferanten in diesem ultimativen Leitfaden.
Learn all about lotion pumps for cosmetic packaging: structure, types, working principles, procurement tips, and quality control. Essential guide for suppliers.
Entdecken Sie die Welt der Rohrdiffusoren und ätherischen Öle! Erfahren Sie, wie Sie die beste Glasflasche, das beste Schilfrohr und die besten Öle für ein entspannendes, aromatisches Zuhause auswählen.
Verwirrt über Druckveredelungen? In diesem Leitfaden werden die Unterschiede zwischen ungestrichenen, matten, glänzenden, wässrigen und UV-Lacken erklärt, damit Sie die beste Lösung für Ihr Projekt finden.
Explore the electroplating process for cosmetic glass packaging—its principles, advantages, materials, coatings, and applications for enhanced beauty and durability.
Amber glass bottles offer luxury, UV protection, and stability for beauty packaging. Learn about their production, quality control, and benefits for skincare brands.
Single-material all-plastic pumps are revolutionizing cosmetic packaging with eco-friendly, cost-effective, and recyclable designs, driving sustainability and brand appeal.
Discover 10 expert tips to choose the best cosmetic bottles, ensuring quality, durability, and sustainability while enhancing your beauty routine effortlessly.
Glass bottles are the best for hair oil storage due to their non-reactivity, UV protection, and ability to preserve quality, ensuring longer shelf life and better efficacy.
Explore the essential role of spray pumps in cosmetics, covering molding, surface treatment, components, and atomization. Learn how spray pumps enhance product performance and user experience in perfumes, gels, and more.
WhatsApp uns