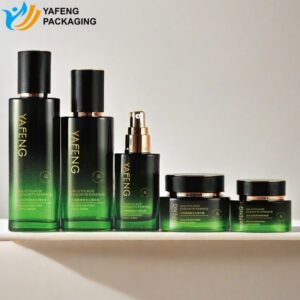
Wiadomości i blog
Wielkie rzeczy w biznesie nigdy nie są dokonywane przez jedną osobę. Robi je zespół ludzi. Mamy tę dynamiczną grupę ludzi
Szklane butelki na balsamy kosmetyczne często pękają podczas napełniania, co nie tylko powoduje straty produktu, ale także stanowi zagrożenie dla jego jakości i bezpieczeństwa. Niniejszy artykuł kompleksowo i dogłębnie analizuje różne przyczyny tego problemu, obejmując wiele czynników, takich jak ciśnienie wewnętrzne i ciśnienie zewnętrzne, oraz rozwija mechanizm wpływu każdego czynnika poprzez rzeczywiste przypadki i dane. Jednocześnie zaproponowano szereg ukierunkowanych rozwiązań, które pomogą producentom kosmetyków skutecznie zmniejszyć częstotliwość pękania ust butelek oraz poprawić wydajność produkcji i jakość produktu.
W dziedzinie produkcji kosmetyków szklane butelki na balsamy stały się preferowanym opakowaniem dla wielu marek ze względu na ich dobrą stabilność, estetykę i właściwości ochrony środowiska. Jednakże, w procesie napełniania, pękanie szklanych butelek z balsamem jest powszechne, co przynosi wiele kłopotów przedsiębiorstwom. Rozwiązanie tego problemu ma kluczowe znaczenie dla poprawy jakości produktu, obniżenia kosztów produkcji i ochrony praw konsumentów. Następnie przyjrzyjmy się bliżej przyczynom pękania ust butelek.
W przypadku szklanych butelek wypełnionych płynami zawierającymi gaz (takimi jak napoje gazowane lub piwo itp.) ciśnienie wewnętrzne będzie nadal rosło podczas napełniania i późniejszego transportu. Na przykład, po napełnieniu napojami gazowanymi, dwutlenek węgla będzie nadal rozpuszczał się i wytwarzał ciśnienie. Gdy ciśnienie wewnątrz butelki przekroczy limit, który może wytrzymać szklana butelka, istnieje ryzyko jej pęknięcia. Ponadto, niektóre emulsje kosmetyczne napełniane na gorąco lub sterylizowane w wysokiej temperaturze, podczas procesu podgrzewania, ze względu na zasadę rozszerzalności cieplnej i kurczenia się, objętość emulsji rozszerza się, powodując wzrost ciśnienia wewnętrznego. Odpowiednie badania wykazały, że gdy ciśnienie wewnętrzne osiągnie 1,5-krotność ciśnienia, które szklana butelka jest w stanie wytrzymać, prawdopodobieństwo pęknięcia znacznie wzrośnie do ponad 80%.
Gdy materiał szklanej szyjki butelki jest niewystarczający, a uszczelka jest zbyt cienka, głowica pompy urządzenia napełniającego może uderzyć w szklane ramię podczas pracy. Zwłaszcza po zakończeniu napełniania, gdy maszyna dokręca głowicę pompy, wywiera ona dodatkowe naprężenie na wąskie gardło, powodując jego pęknięcie. Zgodnie z informacjami zwrotnymi z linii produkcyjnej, w przypadku stosowania szklanych butelek z niewystarczającym materiałem szyjki butelki i cienkimi uszczelkami, problem pęknięcia ujścia butelki spowodowany ciśnieniem zewnętrznym wynosi nawet 30% w niektórych partiach.
Podczas etapu chłodzenia po sterylizacji wysokotemperaturowej szklana butelka doświadcza drastycznego szoku wysokiej i niskiej temperatury. Ze względu na nierówności samego materiału szklanej butelki, stopień rozszerzalności cieplnej i kurczenia się każdej części jest inny, generując w ten sposób naprężenia wewnętrzne. Gdy to wewnętrzne naprężenie przekroczy granicę nośności szklanej butelki, spowoduje to jej pęknięcie. Weźmy jako przykład firmę kosmetyczną. Zanim zoptymalizowano proces chłodzenia, pęknięcie wylotu butelki spowodowane szokiem termicznym stanowiło około 25% wszystkich pęknięć.
W szklanych butelkach występują naprężenia termiczne i strukturalne. Naprężenia termiczne można skutecznie wyeliminować poprzez wtórny proces wyżarzania podczas produkcji szklanych butelek. Jednakże naprężenia strukturalne nie mogą zostać wyeliminowane podczas procesu wyżarzania i pozostaną na stałe w produkcie szklanym. Gdy naprężenia strukturalne przekroczą wytrzymałość mechaniczną samego produktu szklanego, produkt pęknie. Dane z badań pokazują, że ryzyko pęknięcia szklanych butelek z nadmiernymi naprężeniami strukturalnymi jest 5 razy wyższe niż w przypadku normalnych butelek.
Typ butelki szklanej | Prawdopodobieństwo uszkodzenia | Naprężenie wewnętrzne (różnica dróg optycznych) | Jednorodność grubości ścianki butelki | Stabilność termiczna |
---|---|---|---|---|
Zwykła szklana butelka | Około 0,5% | ≤40nm/cm | Lepiej, odchylenie grubości ścianki butelki mieści się w zakresie ±0,2 mm | Może wytrzymać różnicę temperatur wynoszącą około 120 ℃. |
Szklana butelka z nadmiernymi naprężeniami strukturalnymi | Informacje o 20% | ≥80nm/cm | Słabe, odchylenie grubości ścianki butelki może osiągnąć ±0,5 mm | Może wytrzymać tylko różnicę temperatur wynoszącą około 80 ℃. |
Pionowość między dolną powierzchnią szklanej butelki a środkową linią wylotu butelki to odchylenie osi pionowej. Jeśli pionowość szklanej butelki nie jest dobra, odchylenie pozycji jest bardzo prawdopodobne podczas operacji napełniania i zamykania, co doprowadzi do zgniecenia szklanej butelki. W rzeczywistej produkcji wskaźnik pękania szklanych butelek z odchyleniem osi pionowej przekraczającym standardową wartość 0,5 mm podczas napełniania i zamykania może osiągnąć 15%.
Jednorodność grubości ścianek i dna szklanych butelek bezpośrednio określa stopień anizotropii i jest jednym z kluczowych czynników wpływających na odporność na ciśnienie wewnętrzne i szok termiczny. Szklane butelki o nierównej grubości ścianek są podatne na pękanie najpierw w słabych częściach, gdy są poddawane wewnętrznemu ciśnieniu lub zmianom temperatury. Dzięki testom eksperymentalnym na szklanych butelkach o różnej jednorodności grubości ścianek stwierdzono, że odporność na ciśnienie wewnętrzne butelek o słabej jednorodności grubości ścianek jest o około 30% niższa niż w przypadku butelek o dobrej jednorodności.
Podczas procesu napełniania i transportu szklane butelki zderzają się ze sobą. To mechaniczne uderzenie jest doskonałym testem wytrzymałości szklanych butelek. Szklane butelki o słabej odporności na uderzenia są podatne na pęknięcia, a nawet pęknięcia na wylocie butelki i korpusie butelki pod wpływem częstych uderzeń. Na przykład, podczas transportu na duże odległości, szklane butelki, które nie mają odpowiednich środków buforujących, mogą mieć wskaźnik pęknięć 10% - 20% z powodu niewystarczającej odporności na uderzenia.
Wraz ze wzrostem świadomości ekologicznej, ilość butelek szklanych pochodzących z recyklingu rośnie z roku na rok. Jednak wydajność szklanych butelek z recyklingu jest zwykle niższa niż w przypadku nowych butelek. Biorąc za przykład dane dotyczące butelek z recyklingu używanych przez markę kosmetyczną, wskaźnik pęknięć butelek z recyklingu jest o około 40% wyższy niż w przypadku nowych butelek. Głównym powodem jest to, że struktura i wydajność butelek z recyklingu są w różnym stopniu uszkodzone podczas wielokrotnego użytkowania, czyszczenia i transportu.
Przeprojektowanie struktury ust i korpusu szklanej butelki w celu zapewnienia, że jest ona wystarczająco mocna, aby wytrzymać ciśnienie podczas procesu napełniania. Za pomocą środków technicznych, takich jak analiza elementów skończonych, zoptymalizuj kształt i rozkład grubości szklanej butelki, aby zwiększyć stabilność strukturalną. Na przykład zwiększenie grubości wylotu butelki o 1 mm może zwiększyć wytrzymałość na ściskanie wylotu butelki o 20%.
Precyzyjnie kontroluj temperaturę napełniania emulsją, aby dopasować ją do współczynnika rozszerzalności cieplnej szklanej butelki w celu zmniejszenia pęknięcia spowodowanego naprężeniem temperaturowym. Przed napełnieniem należy użyć systemu kontroli temperatury, aby ustabilizować temperaturę emulsji w odpowiednim zakresie. Zgodnie z praktycznym doświadczeniem, kontrolowanie temperatury napełniania na poziomie 25°C - 30°C może skutecznie zmniejszyć ryzyko pęknięcia ust butelki spowodowane problemami z temperaturą.
Należy stosować delikatną i równomierną metodę napełniania, aby uniknąć zbyt szybkiego lub zbyt gwałtownego uderzenia emulsji w otwór butelki. Dostosowując parametry sprzętu do napełniania, należy kontrolować prędkość i ciśnienie napełniania, aby zapewnić równomierny przepływ emulsji do butelki. Rzeczywista produkcja pokazuje, że zmniejszenie prędkości napełniania o 20% może zmniejszyć pęknięcie ust butelki spowodowane uderzeniem napełniania o 50%.
Upewnij się, że korek butelki i rozmiar otworu butelki są dokładnie dopasowane, uszczelnienie jest dobre, a ciśnienie może być równomiernie rozłożone. Sprawdź materiał i strukturę zakrętki i użyj wysokiej jakości materiałów do jej wykonania. Na przykład użycie plastikowych zakrętek do butelek o pewnym stopniu elastyczności i wytrzymałości może skutecznie buforować nacisk na otwór butelki podczas dokręcania.
Przed napełnieniem należy użyć wysoce precyzyjnego sprzętu kontrolnego do przeprowadzenia kompleksowej kontroli jakości szklanych butelek, takiej jak użycie sprzętu do kontroli optycznej w celu sprawdzenia, czy korpus butelki i wylot butelki mają wady i pęknięcia. Dzięki ścisłej kontroli, niekwalifikowane szklane butelki są eliminowane, aby zapobiec ich wprowadzeniu do procesu napełniania. Dane pokazują, że po przeprowadzeniu rygorystycznej kontroli jakości pęknięcia ust butelek spowodowane problemami z jakością szklanych butelek mogą zostać zredukowane o ponad 80%.
Przeprowadzanie systematycznych szkoleń dla operatorów napełniania w celu poprawy ich umiejętności operacyjnych i świadomości jakości. Treść szkolenia obejmuje prawidłowe procedury obsługi sprzętu, techniki napełniania i metody rozwiązywania typowych problemów. Po przeprowadzeniu szkolenia znacznie zmniejszono liczbę uszkodzeń ust butelek spowodowanych czynnikiem ludzkim, a także poprawiono wydajność produkcji.
Po napełnieniu należy użyć odpowiednich materiałów opakowaniowych do ochrony szklanych butelek, takich jak podkładki piankowe, folie bąbelkowe i inne materiały amortyzujące. Podczas transportu należy rozsądnie zaplanować trasę transportu, aby zmniejszyć wstrząsy i wibracje. Praktyka dowiodła, że po podjęciu doskonałych środków ochrony opakowania i transportu, szybkość pękania szklanych butelek na łączu transportowym można kontrolować w granicach 5%.
Problem pęknięcia ust szklanej butelki emulsji kosmetycznej podczas procesu napełniania jest wynikiem połączonego działania wielu czynników, takich jak ciśnienie wewnętrzne, ciśnienie zewnętrzne, szok termiczny, naprężenia wewnętrzne, odchylenie osi pionowej, grubość ścianki, odporność na uderzenia i butelki z recyklingu. Optymalizując konstrukcję butelki, kontrolując temperaturę napełniania, usprawniając proces napełniania, wybierając odpowiednią zakrętkę do butelki, wzmacniając kontrolę jakości, szkoląc operatorów i wykonując dobrą robotę w zakresie pakowania i ochrony transportu, można znacznie zmniejszyć częstość pękania ust butelki, a także poprawić jakość produktu i wydajność produkcji. Każdy producent kosmetyków powinien elastycznie dostosowywać i optymalizować te rozwiązania zgodnie z rzeczywistym środowiskiem produkcyjnym i warunkami, aby skutecznie radzić sobie z problemem pęknięcia ust butelki i zapewnić płynny postęp produkcji.
Poznaj ewoluujący rynek opakowań kosmetycznych! Dowiedz się o rosnących kosztach materiałów, trendach w projektowaniu, ekologicznych rozwiązaniach i strategiach rozwoju marek kosmetycznych.
Poznaj zrównoważony charakter opakowań szklanych, ich możliwości recyklingu i korzyści dla środowiska.
Odkryj zrównoważoną rewolucję w opakowaniach kosmetycznych! Dowiedz się, jak bambus zmienia branżę kosmetyczną dzięki swojemu ekologicznemu, trwałemu i stylowemu wyglądowi.
Odkryj proces flokowania elektrostatycznego w opakowaniach, wzbogacając szklane butelki kosmetyczne o luksusowe tekstury, żywe kolory i przyjazne dla środowiska projekty produktów premium.
Poznaj przyczyny pęknięć szklanych butelek z balsamem kosmetycznym podczas napełniania i odkryj skuteczne rozwiązania poprawiające bezpieczeństwo, jakość i wydajność produkcji.
Odkryj, w jaki sposób powlekanie natryskowe ulepsza opakowania kosmetyków do pielęgnacji skóry i perfum, poprawiając wygląd, tożsamość marki, trwałość i bezpieczeństwo dzięki zaawansowanej technologii.
Poznaj niestandardowe i standardowe butelki do opakowań do pielęgnacji skóry. W tym szczegółowym przewodniku dowiesz się, w jaki sposób rozwiązania Yafeng zwiększają tożsamość marki, jakość i wydajność.
Dowiedz się, jak gradientowy kolor w sprayu przekształca szklane butelki kosmetyczne, poprawia wizerunek marki i zwiększa atrakcyjność produktu dzięki spostrzeżeniom ekspertów z Yafeng Packaging.
Odkryj, jak działa aromaterapia rattanowa i dlaczego szklane butelki są najlepszym wyborem ze względu na długotrwały zapach, bezpieczeństwo i zrównoważone, eleganckie opakowanie.
Odkryj 10 najlepszych rodzajów drewna na nasadki do perfum, porównując teksturę, zalety, wady i cenę, aby pomóc Ci wybrać najlepszy materiał na stylowe, wysokiej jakości opakowanie.
Poznaj szklane butelki kosmetyczne - bezpieczeństwo, korzyści ekologiczne, rodzaje, kolorystykę, koszty formowania, MOQ i wskazówki dotyczące produkcji - w jednym eksperckim, bogatym w dane przewodniku.