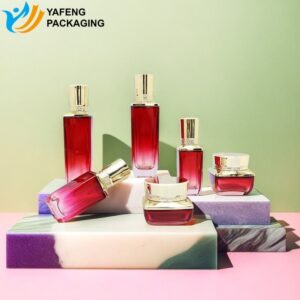
Notícias e blogue
As grandes coisas nos negócios nunca são feitas por uma só pessoa. São feitas por uma equipa de pessoas. Nós temos esse grupo dinâmico de pessoas
Os recipientes de vidro desempenham um papel crucial em várias indústrias, especialmente na cosmética, perfumaria e farmacêutica. Embora ofereçam elegância, durabilidade e proteção, os defeitos de qualidade no fabrico podem comprometer o seu desempenho e apelo estético. Neste artigo, exploramos os defeitos comuns dos recipientes de vidro, suas causas e possíveis soluções.
O fabrico de vidro é um processo complexo e podem ocorrer vários defeitos devido a problemas de matéria-prima, falhas de conceção do molde ou técnicas de moldagem inadequadas. Abaixo estão os defeitos mais comuns encontrados:
As bolhas são bolsas de ar presas na estrutura do vidro. Elas podem aparecer devido a:
Impurezas nas matérias-primas
Fusão ou refinação inadequadas
Composição deficiente do lote
Impacto: Imperfeições estéticas e integridade estrutural reduzida.
As fissuras são fracturas visíveis, enquanto as verificações são fissuras finas na superfície. As causas incluem:
Mudanças bruscas de temperatura durante a produção
Processo de recozimento incorreto
Tensões mecânicas durante o manuseamento
Impacto: Aumento do risco de quebra, tornando o produto inseguro para utilização.
Os recipientes de vidro com espessura de parede inconsistente podem resultar de:
Má conceção do molde
Distribuição desigual do vidro fundido
Processo de conformação incorreto
Impacto: Deficiências estruturais que provocam rupturas sob pressão.
Partículas estranhas incrustadas no vidro, tais como areia não fundida ou materiais refractários, podem surgir devido a:
Matérias-primas contaminadas
Processo de fusão incompleto
Erosão do revestimento do forno
Impacto: Falhas estéticas e potenciais pontos fracos que aumentam a probabilidade de quebra.
Estes defeitos ocorrem devido a:
Atrito durante o transporte ou armazenamento
Manuseamento incorreto
Contacto áspero com peças da máquina
Impacto: Diminuição do atrativo visual e possíveis danos estruturais ao longo do tempo.
Problemas como acabamentos ásperos, pescoços desalinhados ou superfícies de vedação inadequadas são causados por:
Desenhos de moldes defeituosos
Distribuição inconsistente do vidro durante a moldagem
Processos de corte e acabamento deficientes
Impacto: Problemas de fuga, ajuste incorreto do fecho e redução da satisfação do cliente.
Os fabricantes implementam medidas rigorosas de controlo de qualidade para minimizar os defeitos e garantir recipientes de vidro de alta qualidade. As principais estratégias incluem:
Melhoria da seleção de matérias-primas: Utilização de materiais de elevada pureza para minimizar as impurezas e as bolhas.
Operações optimizadas do forno: Assegurar uma fusão e refinação completas para evitar pedras e inclusões.
Manutenção de moldes: Inspeção e manutenção regulares dos moldes para manter a consistência.
Técnicas avançadas de conformação: Aplicação de técnicas precisas de moldagem e de arrefecimento para evitar paredes finas e fissuras.
Tratamento de superfície: Aplicação de revestimentos ou métodos de polimento para reduzir os riscos e aumentar a durabilidade.
Sistemas de Inspeção Automatizados: Utilização de ferramentas de inspeção de alta tecnologia para detetar e eliminar unidades defeituosas antes da embalagem.
Tipo de defeito | Causas | Impacto |
---|---|---|
Defeitos de bolhas | Impurezas, fusão inadequada, composição deficiente do lote | Falhas estéticas, estrutura fraca |
Fissuras e verificações | Mudanças bruscas de temperatura, recozimento deficiente, tensão mecânica | Maior risco de quebra |
Espessura de parede fina/desigual | Má conceção do molde, distribuição desigual do vidro | Fraqueza estrutural, potencial de rutura |
Pedras e inclusões | Matérias-primas contaminadas, fusão incompleta | Questões estéticas, pontos fracos |
Arranhões e abrasões na superfície | Atrito, manuseamento incorreto, contacto áspero com a máquina | Durabilidade e atratividade reduzidas |
Vedação e defeitos de acabamento | Conceção defeituosa do molde, distribuição inconsistente do vidro | Fugas, ajuste incorreto do fecho |
Compreender e tratar os defeitos de qualidade em recipientes de vidro é essencial para manter a integridade do produto, o apelo estético e a satisfação do cliente. Ao implementar medidas robustas de controlo de qualidade e melhorias contínuas no processo de fabrico, as empresas podem garantir a produção de recipientes de vidro de qualidade superior que cumprem as normas da indústria.
Quer seja um fabricante ou uma marca que procura soluções de embalagem fiáveis, a parceria com fornecedores experientes com processos de garantia de qualidade rigorosos pode ter um impacto significativo no sucesso do seu produto no mercado.
Melhore o seu jogo de embalagem com material de embalagem de vidro. Saiba como conseguir um aspeto mate com o nosso guia informativo.
Eleve a sua marca de beleza com um design de embalagem estratégico! Explore as tendências de embalagens de cosméticos de luxo e sustentáveis, colaborações de marcas e experiências de unboxing.
Saiba tudo sobre as bombas de loção para embalagens de cosméticos: estrutura, tipos, princípios de funcionamento, dicas de aquisição e controlo de qualidade. Guia essencial para os fornecedores.
Confuso sobre os acabamentos de impressão? Este guia explica a diferença entre os revestimentos sem revestimento, mate, brilhante, aquoso e UV para o ajudar a escolher o melhor para o seu projeto.
Explore o impacto ambiental das embalagens de vidro e de plástico e faça escolhas informadas e amigas do ambiente.
Explore os frascos personalizados versus frascos de stock para embalagens de produtos para a pele. Saiba como as soluções da Yafeng aumentam a identidade da marca, a qualidade e a eficiência neste guia detalhado.
Descubra como o spray de cor gradiente transforma os frascos de vidro para cosméticos, melhora a imagem da marca e aumenta o atrativo do produto com os conhecimentos especializados da Yafeng Packaging.
Descubra como funciona a aromaterapia de rotim e porque é que os frascos de vidro são a melhor escolha para um aroma duradouro, segurança e uma embalagem sustentável e elegante.
Descubra as 10 melhores madeiras para tampas de perfume, comparando a textura, os prós, os contras e o preço para o ajudar a escolher o melhor material para uma embalagem elegante e de alta qualidade.
Explore as garrafas de vidro para cosméticos - segurança, benefícios ecológicos, tipos, coloração, custos de molde, MOQ e dicas de produção - num guia especializado e rico em dados.
Descubra como garantir uma impressão serigráfica de alta qualidade em frascos de cosméticos e de vidro com métodos de teste especializados, análise de defeitos e normas de fiabilidade.
WhatsApp-nos