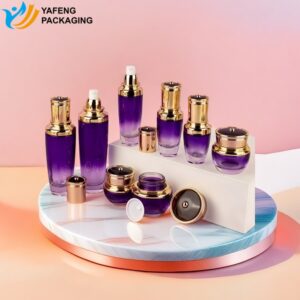
Notícias e blogue
As grandes coisas nos negócios nunca são feitas por uma só pessoa. São feitas por uma equipa de pessoas. Nós temos esse grupo dinâmico de pessoas
Glass bottles are widely used in food, medicine, cosmetics and other industries, but their production process may encounter various quality problems, such as cracks, uneven thickness, deformation and so on. This article will analyze in detail the production process of glass bottles, common problems and how to optimize the production quality. Through data analysis, case studies and citations from authoritative sources, we will provide companies with solutions to improve the production efficiency and quality of glass bottles.
The main raw materials of glass bottles include:
The manufacture of glass bottles usually goes through the following key steps:
Etapa | Process Description |
---|---|
Raw Material Preparation | Crushing and mixing raw materials to ensure glass quality |
Derretimento | Glass is melted in high-temperature kilns or furnaces |
Formação | Using molds to blow or press glass into bottle shapes |
Recozimento | Slowly cooling to remove stress and prevent cracking |
Surface Treatment | Techniques like spraying, etching, and coating to improve durability |
Inspection & Packaging | Quality checks and packaging to ensure product compliance |
Adopt CNC precision machining molds to reduce dimensional errors and improve the consistency of glass bottles.
Introducing robots and AI monitoring system to improve production efficiency and reduce human error.
Cost Item | Percentage |
Raw Materials | 30% |
Energy (Gas, Electricity) | 25% |
Equipment Maintenance | 15% |
Labor Costs | 20% |
Others (Transport, Packaging) | 10% |
Optimizing production quality not only reduces the rate of defective products, but also reduces overall production costs and improves profitability.
Inspection Item | Testing Method |
Crack Detection | High-speed camera + AI analysis |
Thickness Uniformity | Ultrasonic thickness gauge |
Deformation Testing | 3D scanning comparison |
Bubble Content | Transmitted light detection |
A well-known cosmetic brand has reduced the defective rate of glass bottles from 5% to 1% by introducing an intelligent production line, saving more than $500,000 per year in production costs.
Glass bottle production is a complex process involving multiple links, and common problems such as cracks, uneven thickness, deformation, etc. can be optimized and solved by advanced processes and technologies. Enterprises should adopt high-precision molds, intelligent production lines and strict quality control systems to improve product quality and reduce production costs. At the same time, the future of glass bottle manufacturing will be developed in the direction of green and intelligent to enhance market competitiveness.
Descubra como são feitas as garrafas de vidro! Desde as matérias-primas até à moldagem e recozimento, explore o fascinante processo de fabrico deste recipiente quotidiano.
Discover the top 10 women’s perfumes, featuring luxurious scents in elegant glass perfume bottle packaging. Find your perfect fragrance for any occasion today!
Discover the secrets to preserving perfume: how bottle design and temperature control impact fragrance quality. Learn expert tips for optimal storage.
Explore 11 cosmetic packaging surface treatments to enhance aesthetics, durability & branding. Learn their pros, cons & applications to choose the best option.
Explore o intrincado mundo do design de frascos de perfume! Das tampas à base, descubra como cada parte contribui para a experiência da fragrância e a arte da perfumaria.
Explore the electroplating process for cosmetic glass packaging—its principles, advantages, materials, coatings, and applications for enhanced beauty and durability.
Amber glass bottles offer luxury, UV protection, and stability for beauty packaging. Learn about their production, quality control, and benefits for skincare brands.
Single-material all-plastic pumps are revolutionizing cosmetic packaging with eco-friendly, cost-effective, and recyclable designs, driving sustainability and brand appeal.
Discover 10 expert tips to choose the best cosmetic bottles, ensuring quality, durability, and sustainability while enhancing your beauty routine effortlessly.
Glass bottles are the best for hair oil storage due to their non-reactivity, UV protection, and ability to preserve quality, ensuring longer shelf life and better efficacy.
Explore the essential role of spray pumps in cosmetics, covering molding, surface treatment, components, and atomization. Learn how spray pumps enhance product performance and user experience in perfumes, gels, and more.
WhatsApp-nos