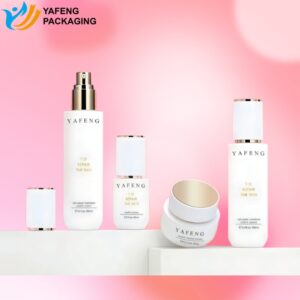
Actualités & Blog
Dans le monde des affaires, les grandes choses ne sont jamais faites par une seule personne. Elles sont le fait d'une équipe. Nous avons ce groupe dynamique de personnes
En matière d'emballage cosmétique, qu'il s'agisse de flacons en plastique ou de contenants en verre, la méthode de distribution du produit joue un rôle crucial dans la satisfaction du consommateur. Les pompes à lotion sont l'un des composants les plus essentiels des contenants cosmétiques, car elles garantissent une distribution efficace du produit. Cet article fournit une vue d'ensemble détaillée des pompes à lotion, couvrant leur définition, leur structure, leur processus de fabrication, leurs principes de fonctionnement et les considérations clés pour l'approvisionnement. Ce guide est conçu pour aider les professionnels de l'approvisionnement de l'industrie cosmétique à prendre des décisions éclairées.
Une pompe à lotion est un outil de distribution utilisé dans les conteneurs de produits cosmétiques pour délivrer efficacement des produits liquides tels que des sérums, des crèmes et des lotions. Elle fonctionne selon le principe de l'équilibre atmosphérique : en appuyant sur la tête de la pompe, le produit est expulsé tout en permettant à l'air de pénétrer dans le récipient pour maintenir l'équilibre de la pression. Ce mécanisme garantit une distribution fluide et régulière, améliorant ainsi l'expérience de l'utilisateur.
Les pompes à lotion sont composées de plusieurs éléments, chacun jouant un rôle essentiel dans leur fonctionnement. Vous trouverez ci-dessous une description de leur structure et de leur processus de fabrication :
1. Composants structurels
Une pompe à lotion standard comprend généralement les éléments suivants :
Tête de pompe/actionneur
Tige de pompe supérieure
Capuchon de verrouillage
Joint d'étanchéité
Bouchon de bouteille
Corps de pompe
Tige de pompe inférieure
Printemps
Corps de pompe
Boule de verre
Tube plongeur
Les composants spécifiques peuvent varier en fonction de la conception et de l'utilisation prévue de la pompe, mais l'objectif principal reste le même : distribuer le produit de manière efficace.
2. Processus de fabrication
La plupart des composants des pompes à lotion sont fabriqués à partir de matières plastiques telles que le PE (polyéthylène), le PP (polypropylène) et le PEBD (polyéthylène basse densité) par moulage par injection. Certaines pièces comme les billes de verre, les ressorts et les joints sont souvent sous-traitées. La tête et le collet de la pompe peuvent être personnalisés à l'aide de procédés tels que la galvanoplastie, le revêtement en aluminium, la pulvérisation ou le moulage par injection en couleur. En outre, la surface de la tête de pompe et du collier peut être décorée à l'aide de techniques d'impression telles que le marquage à chaud, la sérigraphie ou la tampographie.
Les pompes à lotion existent en différents types et modèles, chacun adapté à des applications spécifiques. Voici un aperçu de leur classification et de leur mécanisme de fonctionnement :
1. Classification des produits
Par diamètre : Les tailles courantes sont les suivantes : Ф18, Ф20, Ф22, Ф24, Ф28, Ф33 et Ф38.
Par mécanisme de verrouillage : Les options comprennent des serrures à bloc de guidage, des serrures filetées, des serrures à clip et des conceptions sans serrure.
Par structure : Les catégories comprennent les pompes à ressort externes, les pompes à ressort en plastique, les pompes résistantes à l'eau et les pompes à haute viscosité.
Par méthode de distribution : Bouteilles sous vide et systèmes de tubes plongeurs.
Par volume de distribution : Gammes de 0,15/0,2cc à 10cc et plus.
2. Principe de fonctionnement
Lorsque l'on appuie sur la tête de pompe, le volume de la chambre à ressort diminue, ce qui augmente la pression. Le liquide est alors poussé à travers la valve vers la buse, où il est distribué. Le relâchement de la tête de pompe crée un vide, permettant au liquide du récipient de remplir à nouveau la chambre à ressort. Ce cycle assure une distribution régulière et contrôlée.
3. Mesures de performance
Les principaux indicateurs de performance des pompes à lotion sont les suivants
Nombre de presses vides
Volume de distribution
Force de pression
Couple nécessaire pour ouvrir la tête de pompe
Vitesse de rebond
Capacité de prise d'eau
4. Ressorts internes et externes
Les ressorts externes sont préférés dans de nombreuses conceptions car ils n'entrent pas en contact avec le produit, ce qui élimine le risque de contamination par la rouille.
Lors de l'achat de pompes à lotion pour emballage cosmétiquePlusieurs facteurs doivent être pris en compte pour garantir la qualité et la fonctionnalité :
1. Les applications
Les pompes à lotion sont largement utilisées dans l'industrie cosmétique pour des produits tels que les shampooings, les gels douche, les crèmes hydratantes, les sérums, les crèmes solaires, les crèmes BB, les fonds de teint, les nettoyants pour le visage et les désinfectants pour les mains.
2. Sélection des fournisseurs
Choisissez des fournisseurs qui ont fait leurs preuves et qui ont la réputation de fournir des pompes à lotion de haute qualité. Assurez-vous qu'ils respectent les normes industrielles et qu'ils peuvent répondre à vos besoins spécifiques.
3. Compatibilité des produits
Vérifiez que la pompe est compatible avec votre conteneur en termes de taille, d'étanchéité et de conception générale. Cela permet d'assurer un bon fonctionnement et d'éviter les fuites.
4. Stabilité de la chaîne d'approvisionnement
Évaluez la capacité de production et les délais de livraison du fournisseur afin d'éviter toute perturbation de votre processus de fabrication.
5. Structure des coûts
Le coût des pompes à lotion est influencé par :
Coûts des matériaux : Y compris les plastiques, le caoutchouc et l'acier inoxydable.
Coûts de fabrication : Comme la création de moules, le moulage par injection et l'assemblage.
Coûts d'emballage et de transport : Y compris les matériaux d'emballage et la logistique.
6. Contrôle de la qualité
Mettre en œuvre des mesures strictes de contrôle de la qualité, notamment
Inspection des matières premières : S'assurer que les matériaux sont conformes aux spécifications requises.
Contrôle des processus de fabrication : Contrôler les dimensions des moules et les processus d'assemblage.
Test du produit : Effectuer des essais de pression, des essais d'étanchéité et des essais fonctionnels.
Systèmes de gestion de la qualité : Mettre en place des systèmes solides pour maintenir la cohérence et la fiabilité.
Tableau 1 : Tailles et applications courantes des pompes à lotion
Diamètre (mm) | Applications courantes |
---|---|
Ф18 | Sérums, essences |
Ф20 | Lotions légères |
Ф24 | Crèmes hydratantes |
Ф28 | Lavages corporels |
Ф38 | Shampooings |
Tableau 2 : Principaux indicateurs de performance des pompes à lotion
Métrique | Description |
---|---|
Volume de distribution | Quantité de produit distribuée par pompe |
Force de pression | Force nécessaire pour activer la pompe |
Vitesse de rebond | Vitesse de réarmement de la tête de pompe |
Capacité de prise d'eau | Capacité à prévenir les infiltrations d'eau |
Tableau 3 : Ventilation des coûts pour les pompes à lotion
Élément de coût | Pourcentage du coût total |
---|---|
Coûts des matériaux | 40% |
Coûts de fabrication | 35% |
Emballage et logistique | 25% |
10 points clés pour l'achat de pompes à lotion
Comprendre la structure et les composants des pompes à lotion pour garantir la compatibilité avec votre produit.
Choisissez le bon type de pompe en fonction de la viscosité de votre produit et des exigences de distribution.
Privilégiez les fournisseurs qui jouissent d'une solide réputation et dont les chaînes d'approvisionnement sont fiables.
Vérifiez la compatibilité du produit avec votre conteneur afin d'éviter les fuites et d'assurer son fonctionnement.
En fonction de la sensibilité de votre produit, envisagez des ressorts internes et externes.
Évaluer les paramètres de performance tels que le volume de dépose et la force de pression.
Mettre en œuvre des mesures strictes de contrôle de la qualité pour maintenir la cohérence des produits.
Tenez compte des coûts des matériaux, de la fabrication et de la logistique lors de l'établissement du budget.
Tester les pompes pour vérifier leur résistance à la pression, leur étanchéité et leur fonctionnalité avant de finaliser les commandes.
Restez au courant des tendances et des innovations de l'industrie de l'emballage cosmétique.
En gardant ces points à l'esprit, vous pouvez vous assurer que votre emballage cosmétique répond aux normes fonctionnelles et esthétiques, améliorant ainsi l'expérience globale du consommateur.
Découvrez comment garantir une sérigraphie de haute qualité sur les flacons de cosmétiques et de verre grâce à des méthodes de test expertes, à l'analyse des défauts et à des normes de fiabilité.
Découvrez le monde des diffuseurs à roseaux et des huiles essentielles ! Apprenez à choisir le meilleur flacon en verre, les meilleurs roseaux et les meilleures huiles pour créer une maison aromatique et relaxante.
Découvrez les pompes pour pulvérisateurs : types, utilisations et comment choisir celle qui convient le mieux à vos besoins.
Découvrez pourquoi l'emballage en verre est essentiel pour la conservation des produits de soin de la peau, car il offre durabilité, sécurité et esthétique de premier ordre.
Découvrez un guide complet sur les flacons compte-gouttes en verre - du matériau et de la forme à la personnalisation et à l'utilisation - pour des solutions d'emballage de liquides précises, durables et haut de gamme.
Découvrez les flacons personnalisés par rapport aux flacons standard pour l'emballage des produits de soin de la peau. Découvrez comment les solutions de Yafeng renforcent l'identité de la marque, la qualité et l'efficacité dans ce guide approfondi.
Découvrez comment les sprays de couleur dégradée transforment les flacons cosmétiques en verre, améliorent l'image de la marque et renforcent l'attrait du produit grâce aux conseils d'experts de Yafeng Packaging.
Découvrez comment fonctionne l'aromathérapie au rotin et pourquoi les flacons en verre sont le meilleur choix pour une odeur durable, la sécurité et un emballage durable et élégant.
Découvrez les 10 meilleurs bois pour les bouchons de parfum, en comparant la texture, les avantages, les inconvénients et le prix pour vous aider à choisir le meilleur matériau pour un emballage élégant et de haute qualité.
Découvrez les flacons en verre pour cosmétiques - sécurité, avantages écologiques, types, coloration, coûts de moulage, MOQ et conseils de production - dans un guide riche en données et rédigé par des experts.
Découvrez comment garantir une sérigraphie de haute qualité sur les flacons de cosmétiques et de verre grâce à des méthodes de test expertes, à l'analyse des défauts et à des normes de fiabilité.
Nous contacter par WhatsApp