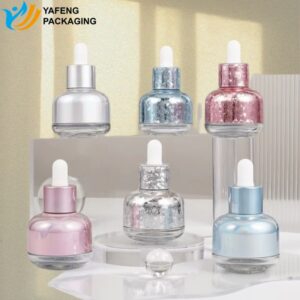
News & Blog
Great things in business are never done by one person. They’re done by a team of people. We have that dynamic group of peoples
This article provides an in-depth look into the fascinatingย glass bottle manufacturing process. From raw materials to finished product, we’ll explore howย glass bottles are made, revealing the intricate steps involved in transforming simple ingredients into the ubiquitousย containersย we use every day. This comprehensive guide is worth reading for anyone curious about theย manufacturing of glass, offering insights into the technology, precision, and artistry behind everyย glass bottleย andย jarย that lines our shelves.
The journey of aย glass bottleย begins with a precise blend ofย raw materials. The primary ingredient isย silicaย sand, which forms the basic structure of theย glass. However,ย silicaย alone has a very highย melting point, making it impractical forย glass manufacturing. To overcome this,ย soda ashย is added to lower theย melting point, making theย process of making glassย more manageable.
Limestoneย is another crucial component, added to enhance the chemicalย stability of the glass, preventing it from dissolving in water. In addition to these primary ingredients,ย recycled glass, also known asย cullet, is often used.ย Culletย not only reduces waste but also lowers the energy required for melting, making theย process more energy-efficient. The precise proportions of theseย raw materialsย are carefully controlled to achieve the desired properties of the finishedย glass bottle, such as color, clarity, and durability.ย Glass is madeย of these.
Theย raw materialsย are thoroughly mixed and then fed into aย furnace, where they are subjected to intense heat, typically around 1700ยฐC (3100ยฐF). This is theย melting processย that transforms the granular mixture intoย molten glass, a viscous, glowing liquid. The intense heat causes theย raw materialsย to fuse, forming a homogenous liquid. Theย furnaceย operates continuously,ย 24 hours a day, 7 days a week, to maintain the high temperatures required forย glass manufacturing.
Inside theย furnace, theย molten glassย undergoes a refining process to remove anyย air bubblesย or impurities. This is crucial for ensuring the clarity and strength of the finishedย glass bottles. Theย melting processย is a critical stage in theย glass bottle manufacturingย journey, laying the foundation for the subsequent forming stages.ย Glass is createdย in this process.
Once theย glassย is melted and refined, it’s ready for theย forming process, where it takes on the familiar shape of aย bottleย orย jar. There are different methods used, like for example,ย press and blow method. Theย glass manufacturing processย can vary. One common technique is the “blow and blow” process, primarily used for narrow-neckย containers. In this method, aย gobย ofย molten glassย is delivered to a mold, andย compressed airย is used to form a hollow cavity, creating theย parison, a preliminaryย bottle shape. Theย parison is then flippedย and transferred to a second mold, where another blast of air expands it to the finalย bottle shape.
Another widely used method is the “press and blow” process, often preferred for wide-mouthย glass jarsย and some types ofย bottles. In this technique, aย plungerย is used to press theย gobย ofย molten glassย into theย parisonย mold, forming the basic shape. Theย parisonย is then transferred to a blow mold, whereย compressed airย is used to expand it to its final form. Thisย process allows the glassย to be shaped. Bothย bottles and jarsย use these methods. Theย press and blow processย creates a more uniform distribution ofย glass, resulting in aย containerย with greater strength and dimensional accuracy.
Process | Description | Container Type | Advantages | Disadvantages |
---|---|---|---|---|
Blow and Blow | Aย gobย ofย molten glassย is formed into aย parisonย using compressed air. Theย parisonย is then transferred to a blow mold and blown into its final shape using compressed air. | Narrow-neck bottles | Good for intricate designs, produces lighter bottles | Less control overย glassย distribution, can result in weakerย bottles, not suitable for wide-mouth |
Press and Blow | Aย plungerย presses aย gobย ofย molten glassย into aย parison. Theย parisonย is then transferred to a blow mold and blown into its final shape using compressed air. Theย press and blow processย is very effective. | Wide-mouth jars, some bottles | More uniformย glassย distribution, strongerย bottles, better dimensional accuracy | Can be slower than blow and blow, may not be suitable for very intricate designs |
Narrow-Neck Press and Blow (NNPB) | A variation of press and blow specifically for narrow-neck bottles. A smaller, more precise plunger is used to form the parison, giving greater control over glass distribution in the neck and shoulder area. | Narrow neck bottles | Lighter bottles with good strength and precise dimensions | More complex and may require more specialized equipment |
After theย forming process, the newly formedย glass bottlesย are still hot and containย internal stressย that could cause them to crack or shatter. To relieve this stress, theย bottlesย undergo a crucial process calledย annealing. This involves passing theย bottlesย through a long, temperature-controlled oven called a lehr. This is a very important part ofย glass bottle production.
In the lehr, theย glass bottlesย are gradually cooled down over a specific period. This slow coolingย process allows the glassย to solidify uniformly, reducingย internal stressย and increasing the strength and durability of theย glass. Theย annealing processย is essential for ensuring that theย glass bottlesย can withstand the rigors of filling, transportation, and everyday use.ย Annealย is crucial for theย glass.
Quality controlย is paramount inย glass bottle manufacturing. Throughout theย production process, from the initial mixing ofย raw materialsย to the final packaging, rigorous inspections and tests are conducted to ensure that theย glass bottlesย meet the required standards. This includes checking forย defects such as cracks, bubbles, or variations in wall thickness. Also checking for any type ofย glass surfaceย problems.
Automated inspection systems, using cameras and sensors, are often employed to detect even the most minor imperfections. These systems can identifyย defects that might be missed by the human eye, ensuring that onlyย quality glassย products reach the consumer.ย Glass bottlesย that fail to meet the quality standards are rejected and often recycled back into theย processย asย cullet, further emphasizing the industry’s commitment to sustainability.ย Glass is cutย if there are any problems.ย Glass is non-toxicย and safe.
While the basic ingredients forย glassย remain relatively consistent, different types ofย glassย can be created by varying the composition and manufacturingย process. Soda-limeย glassย is the mostย widely usedย type forย bottles and jars, owing to its versatility, affordability, and recyclability. This is a very popularย type of glass. It’s theย glassย we commonly encounter in everyday items likeย wine bottles, foodย jars, and beverageย containers.
Borosilicateย glass, known for its exceptional resistance to thermal shock, is often used for laboratory glassware and some specialtyย containersย that require high heat resistance. Another type is temperedย glass, which undergoes a special heat treatment to increase its strength and make it shatter into small, relatively harmless pieces if broken. This makes it suitable for applications where safety is a primary concern. Choosing the right type depends on the intended use of theย containerย and the properties required. This is whereย quality glassย is important.
Cullet, orย recycled glass, plays a vital role in sustainableย glass bottle manufacturing. Usingย recycled glassย in theย production processย offers several environmental benefits. Firstly, it reduces the demand forย raw materials, conserving natural resources. Secondly,ย culletย melts at a lower temperature than theย raw materials, meaning that less energy is required in theย furnace, leading to lower greenhouse gas emissions.
Incorporatingย culletย into theย glassย mixture can also make theย process of meltingย more efficient. Theย glass industryย actively promotes the use ofย recycled glass, and manyย glass bottle manufacturersย strive to maximize the proportion ofย culletย in their production. This commitment to usingย recycled glassย demonstrates the industry’s dedication to environmental responsibility and contributes to a more circular economy forย glass packaging. In many cases,ย shredded glass piecesย are used asย cullet.ย Culletย is added to theย furnaceย at the same time as the other materials that will make up theย glass mixture.
The journey from theย furnaceย to the finishedย glass bottleย is a remarkable transformation.ย Molten glass, a glowing liquid, is carefully metered out in precise portions calledย gobs. The size and weight of theย gobย are critical, as they determine the final dimensions of theย glass container. Theย gobย is like aย stream of molten glass. Theseย gobsย are then guided through chutes and into the forming machines, where the magic happens.
In the forming machines, whether it’sย blow and blow processย orย press and blow process, theย gobย is rapidly shaped into aย bottleย orย jar. Thisย formation processย requires precise timing and control of temperature and airflow. The molds used in these machines are meticulously crafted to ensure that eachย glass bottleย meets the exact specifications. This is theย basic shape of the bottle. The speed and efficiency of this transformation are a testament to the advanced engineering involved in modernย glass bottle manufacturing. It takes between 9-12 seconds to make aย glass bottle.
Stage | Description | Key Considerations |
---|---|---|
Raw Material Mixing | Silica sand, soda ash, limestone, and cullet are precisely weighed and mixed. | Accurate proportions are crucial for the desired glass properties (clarity, strength, color). |
Melting | The raw material mixture is heated in a furnace to around 1700ยฐC (3100ยฐF), transforming it into molten glass. | Temperature control is vital for complete melting and refining. Air bubbles and impurities must be removed. |
Gob Formation | Molten glass is metered out in precise portions called gobs. | Gob weight and temperature are critical for consistent bottle dimensions. |
Forming | Gobs are fed into molds and shaped into bottles or jars using either the blow and blow or press and blow process.ย B&B processย is also used. This is the most important step inย glass manufacturing. | Precise timing, temperature control, and airflow are essential for proper shaping and to avoid defects.ย Process and NNPBย are two different methods of forming the bottles. |
Annealing | Newly formed bottles are slowly cooled in a lehr (annealing oven) to relieve internal stress. | Controlled cooling rate prevents cracking and ensures the strength and durability of the glass. |
Inspection | Bottles are inspected for defects (cracks, bubbles, dimensional variations) using automated systems and manual checks. | Rigorous quality control ensures only flawless bottles reach the market. |
Packaging | Approved bottles are packaged for shipment to customers. | Proper packaging protects bottles during transportation and storage. |
Theย glass bottle manufacturingย industry continues to evolve, driven by innovation and a growing focus onย sustainability.ย Manufacturers of glassย are constantly researching and developing new technologies to improve efficiency, reduce environmental impact, and meet the changing needs of consumers. Theย glass bottle manufacturing processย is constantly being improved. This includes exploring advanced forming techniques that allow for more intricateย bottleย designs and lighter-weightย containers. There is also ongoing research into alternative materials and coatings that can further enhance the performance andย sustainabilityย ofย glass packaging. This will help theย production of glass bottles.
One area of focus is the development of even more energy-efficientย furnacesย and processes. This includes exploring the use of alternative fuels, optimizing heat recovery systems, and implementing advanced process control technologies. The industry is also committed to increasing the use ofย recycled glass, with a goal of achieving a closed-loop system whereย glass bottlesย are recycled back into newย glass containersย indefinitely. These advancements will ensure thatย glassย remains a preferred packaging material for its aesthetic appeal, functionality, andย sustainability. Usingย glassย is good for the environment.
Glass bottlesย are ubiquitous in our lives, yet we rarely consider the intricateย processย that goes into their creation.ย Understanding the glass bottleย means appreciating the complex interplay of science, technology, and artistry involved inย glass bottle manufacturing. From the careful selection ofย raw materialsย to the precise control of theย meltingย and forming processes, every step plays a crucial role in shaping the final product. Theย process of making glass bottlesย is not simple.
The journey of aย glass bottleย is a testament to human ingenuity and our ability to transform simple materials into objects of both beauty and utility. As consumers, understanding howย glass bottles are madeย can inform our choices and encourage us to appreciate the value ofย glass packaging. By recognizing the importance ofย recyclingย and supporting sustainable practices in theย glass industry, we can contribute to a more environmentally responsible future for this versatile and enduring material. This article gave a good overview of theย glass manufacturing process.
Here are the 10 most important things to remember aboutย glass bottle manufacturing:
Discover the pros and cons of glass and plastic packaging. Make informed decisions for sustainability, cost, and brand image in skincare and beyond.
Discover the world of reed diffusers & essential oils! Learn how to choose the best glass bottle, reeds, & oils for creating a relaxing aromatic home.
Explore the intricacies of glass bottle mold production, from types and processes to technical distinctions, highlighting innovations driving precision, scalability, and cost efficiency.
Unlock the secrets to shipping cosmetics internationally! Get expert tips on packaging, customs, regulations, and choosing carriers like DHL Express for safe and efficient delivery.
Discover the differences between pumps and sprays in cosmetic packaging. Choose the best option for your product!
Explore custom vs. stock bottles for skincare packaging. Learn how Yafengโs solutions boost brand identity, quality, and efficiency in this in-depth guide.
Discover how gradient color spray transforms cosmetic glass bottles, enhances brand image, and boosts product appeal with expert insights from Yafeng Packaging.
Discover how rattan aromatherapy works and why glass bottles are the best choice for long-lasting scent, safety, and sustainable, elegant packaging.
Discover the top 10 woods for perfume caps, comparing texture, pros, cons, and price to help you choose the best material for stylish, high-quality packaging.
Explore cosmetic glass bottlesโsafety, eco benefits, types, coloring, mold costs, MOQ, and production tipsโin one expert, data-rich guide.
Discover how to ensure high-quality silk screen printing on cosmetic and glass bottles with expert testing methods, defect analysis, and reliability standards.
WhatsApp us