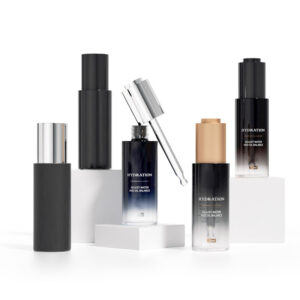
Nachrichten & Blog
Großartige Leistungen in der Wirtschaft werden nie von einer einzelnen Person erbracht. Sie werden von einem Team von Menschen vollbracht. Wir haben diese dynamische Gruppe von Menschen
At a time when competition in the cosmetics industry is becoming increasingly fierce, the appearance and performance of cosmetic glass packaging have become key factors in attracting consumers. The surface coating process is like a magic that gives glass packaging materials a unique charm. It can not only make cosmetic glass bottles, Parfümflaschen aus Glas, glass cream jars, lotion bottles, lotion bottles and other packaging materials colorful and visually attractive, but also enhance their corrosion resistance and wear resistance. This article will deeply analyze the principles, system composition, basic process flow and application of the surface coating process of cosmetic glass packaging materials in the field of cosmetic packaging materials. Through detailed data and comparison, it will unveil the mystery of this process for you.
Spraying, as an indispensable coloring process after the cosmetic glass packaging materials are formed, disperses the coating into uniform and fine droplets under the action of pressure or centrifugal force through a spray gun or a disc atomizer, and accurately applies it to the surface of the glass packaging material. It is like a gorgeous coat tailored for glass packaging, making ordinary glass instantly dazzling.
Spraying technology can be divided into many forms, the most common ones are air spraying, airless spraying, electrostatic spraying, and derived methods such as high-flow low-pressure atomization spraying, thermal spraying, automatic spraying, and multi-group spraying. Different spraying methods are suitable for cosmetic glass packaging materials of different types and needs. For example, air spraying is suitable for glass perfume bottles and lotion bottles with high surface quality requirements and complex shapes, and can achieve a delicate and uniform coating effect; while electrostatic spraying performs well in improving coating utilization and production efficiency, and is often used in large-scale production of cosmetic glass bottles and lotion bottles.
Protective function: Cosmetic glass packaging materials will be eroded by various factors such as light, humid air, and cosmetic ingredients during daily use. The spraying process can effectively isolate these erosive media and protect the glass from damage by covering a layer of coating on the glass surface. According to relevant research data, the corrosion resistance of cosmetic glass packaging materials treated with spraying can be improved by 30% – 50%, and the wear resistance can be improved by 20% – 40%, which greatly extends the service life of the packaging materials. For example, for glass cream jars, the protective layer after spraying can prevent the oil components in the cream from corroding the glass and maintain the integrity of the packaging materials.
Decorative function: In the era of appearance economy, the appearance design of cosmetics is crucial. The spraying process can give cosmetic glass packaging materials a rich variety of colors, gloss and texture to meet consumers’ pursuit of beauty. Whether it is a crystal clear glass perfume bottle or a colorful lotion bottle, the spraying process can achieve a unique visual effect and enhance the attractiveness of the product. A survey shows that cosmetics with exquisite appearance have a 20% – 30% higher sales volume in the market than those with ordinary appearance.
Special functions: In addition to the basic protection and decorative functions, the spraying process can also give cosmetic glass packaging materials special functions. For example, special coatings with fireproof, waterproof and anti-fouling functions applied on the glass surface can make cosmetics safer and more convenient during use; temperature-indicating coatings applied on the glass surface can display the storage temperature of cosmetics through color changes to ensure product quality; and luminous and reflective coatings can make cosmetics more eye-catching at night or in specific environments, improving product recognition.
Air conditioning system: provides clean and fresh air that has been treated with temperature, humidity and dust removal for the spraying room. Appropriate temperature and humidity can ensure the drying speed and coating quality of the coating, while clean air can prevent dust and other impurities from adhering to the surface of the glass packaging material and affecting the spraying effect. Generally speaking, the temperature of the spraying room is controlled at 20℃ – 25℃, and the relative humidity is preferably maintained at 40% – 60%.
Spraying room body: It consists of a dynamic pressure chamber, a static pressure chamber, a spraying operation room and a grille bottom plate. The design of the dynamic pressure chamber and the static pressure chamber can make the air evenly distributed, providing a stable airflow environment for the spraying operation; the spraying operation room is the space where the spraying operation is actually carried out; the grille bottom plate is used to collect the paint mist and coating that falls during the spraying process.
Exhaust and paint mist capture system: Through the paint mist capture device, exhaust fan and air duct and other equipment, the paint mist generated during the spraying process is discharged from the spraying room in time, and the paint mist is effectively captured to prevent environmental pollution. Common paint mist capture devices include water curtain type and water vortex type, and their paint mist capture efficiency can reach more than 90%.
Waste paint removal device: It is responsible for timely removing the waste paint residue in the sewage discharged from the exhaust washing device of the spraying room, and returning the filtered water to the ditch at the bottom of the spraying room for recycling, which not only saves water resources but also reduces the discharge of waste paint.
The coating line is mainly composed of seven parts, including pre-treatment equipment, powder spraying system, paint spraying equipment, oven, heat source system, electronic control system, and hanging conveyor chain.
Pre-treatment equipment: For cosmetic glass packaging materials, the purpose of pre-treatment is to remove impurities such as oil and dust on the surface, and to roughen the surface to enhance the adhesion of the coating. The spray-type multi-station pre-treatment unit is a commonly used equipment, and its typical process includes pre-degreasing, degreasing, water washing, water washing, surface conditioning, phosphating, water washing, water washing, pure water washing and other steps. For some special glass packaging materials, such as glass perfume bottles with complex patterns, shot blasting machines may also be used for treatment. This method has no water pollution and is suitable for glass parts with simple structure, severe rust, no oil or little oil.
Powder spraying system: The small cyclone + filter element recovery device in powder spraying is a more advanced powder recovery device with fast color change speed, which can meet the diverse color requirements of cosmetic glass packaging materials. It is recommended to use imported products for the key parts of the powder spraying system to ensure the quality and stability of the spraying, while the powder spraying room, electric mechanical lift and other parts can use domestic products to reduce costs.
Painting equipment: Oil spraying room and water curtain spraying room are widely used in the surface coating of cosmetic glass packaging materials. They can effectively capture paint mist and ensure the cleanliness of the spraying environment. They are suitable for the coating of large objects such as bicycles and automobile leaf springs, and are also suitable for the mass production of cosmetic glass packaging materials.
Oven: The oven is an important equipment in the coating production line, and its temperature uniformity directly affects the coating quality. The heating methods of the oven include radiation, hot air circulation and radiation + hot air circulation. The hot air circulation oven has good thermal insulation, uniform temperature in the oven, and less heat loss. After testing, the temperature difference in the oven is less than ±3oC, reaching the performance indicators of similar products in advanced countries, which can ensure that the cosmetic glass packaging materials are heated evenly during the drying process to avoid problems such as cracking and shedding of the coating.
Heat source system: Hot air circulation is a commonly used heating method. It uses the principle of convection conduction to heat the oven to achieve the drying and curing of the workpiece. The heat source can be selected from electricity, steam, gas or fuel oil according to the specific situation of the user. If the circulating fan that produces the heat source is a special high-temperature resistant fan, it has the advantages of long life, low energy consumption, low noise, and small size, which can reduce production costs and improve production efficiency.
Electrical control system: There are two ways of electrical control of the coating assembly line: centralized and single-column control. Centralized control uses a programmable controller (PLC) to control the host, automatically controls each process according to the compiled control program, realizes data collection and monitoring alarm, and is suitable for large-scale and highly automated production; single-column control is a single-column control of each process, and the electric control box (cabinet) is set near the equipment. It has low cost, intuitive operation, and convenient maintenance. It is often used in small production enterprises.
Suspension conveyor chain: The suspension conveyor is a conveying system for industrial assembly lines and coating lines. The accumulation type suspension conveyor is suitable for the coating line of cosmetic glass packaging materials. The workpiece is hoisted on a special hanger, and the in and out turnouts are smooth. The turnouts are opened and closed by electrical control according to the work instructions, which can meet the automatic transportation of the workpieces in each processing station. The workpieces are cooled in parallel in the strong cooling room and the lower part area, and a hanger identification and traction alarm shutdown device is set in the strong cooling area to ensure the safety and stability of the production process.
As a tool for atomizing and spraying paint on the surface of glass packaging materials, the performance and quality of the spray gun directly affect the spraying effect. Different types of spray guns are suitable for different spraying processes and coatings. For example, air spray guns are suitable for fine spraying of low-viscosity coatings, which can achieve uniform and delicate coatings; while high-pressure airless spray guns are suitable for rapid spraying of high-viscosity coatings, with high efficiency and suitable for large-area coating.
Coatings are key materials for protecting and decorating the surface of cosmetic glass packaging materials. After being applied to the glass surface, they form a continuous coating film with certain functions and firm adhesion. The functions of coatings mainly include protection, decoration and special functions. In the field of cosmetic glass packaging materials, different types of coatings are suitable for different needs. For example, for glass cream jars and lotion bottles that require high gloss and wear resistance, polyurethane coatings can be used; for glass perfume bottles and lotion bottles that require good chemical resistance and weather resistance, acrylic coatings are a good choice.
There are differences in the coating process and process of different targets. Taking the common plastic parts coating process as an example, its process also has a certain reference significance for the coating of cosmetic glass packaging materials.
Pre-degreasing: Partially pre-degrease the surface of the glass packaging material to remove most of the oil and impurities on the surface, and prepare for the subsequent degreasing process.
Main degreasing: Use a cleaning agent to thoroughly degrease the surface of the glass packaging material to ensure that the surface is clean and free of oil.
Water washing: After two water washing processes, use clean tap water to rinse the chemical reagents remaining on the glass surface. The water temperature for water washing is room temperature (RT), and the spray pressure is 0.06 – 0.12Mpa. Then, pure water washing is carried out, and the glass surface is thoroughly cleaned with fresh deionized water. The purity requirement of deionized water is conductivity ≤10μm/cm to ensure that there is no impurity residue on the glass surface.
Air blowing area: The air duct after pure water washing in the water washing channel is used to blow off the water droplets remaining on the glass surface with strong wind. However, due to the structural characteristics of glass packaging materials, water droplets in some parts may not be completely blown off, and the drying area cannot dry the water droplets. Therefore, the surface of the workpiece needs to be checked after flame treatment. When water accumulation occurs, the glass surface needs to be wiped.
Drying: The product drying time is generally 20 minutes. The oven uses gas heating circulating air to make the temperature in the drying channel reach the set value. When the washed and dried product passes through the oven channel, the hot air dries the moisture on the surface of the product. The setting of baking temperature needs to comprehensively consider the evaporation rate of water on the product surface and the heat resistance of the glass packaging material to avoid deformation or damage of the glass due to excessive temperature.
Flame treatment: Use a strong oxidizing flame to oxidize the glass surface, increase the surface tension of the glass substrate surface, so that the paint can better combine with the substrate surface, thereby improving the adhesion of the paint. This step is crucial to improving the adhesion of the paint on the glass surface.
Primer: The purpose of primer is diverse, mainly including increasing the adhesion of the paint to the glass surface, reducing color difference, and masking the bad points of the workpiece. Although the appearance of the primer is not easy to detect, it has an important impact on the quality and performance of the entire coating.
Mid-coat: Mid-coat is a coating film that shows color after coating. It not only makes the appearance of the glass packaging material more beautiful, but also gives the coating film good physical and chemical properties, such as hardness and wear resistance.
Top coating: Top coating is the last coating layer in the coating process. Its purpose is to give the coating film high gloss and excellent physical and chemical properties, protect the glass packaging material from external factors, and improve the overall texture and grade of the product.
Spraying technology is widely used in the field of cosmetic packaging. It is one of the main coloring treatment processes for external components of products such as lipstick kits, cosmetic glass bottles, pump heads, and bottle caps. Whether it is a delicate and small glass perfume bottle, the spraying process can present elegant colors and unique gloss, enhancing the high-end texture of the perfume; or a large-capacity glass cream jar and lotion bottle, the spraying process can enhance its wear resistance and corrosion resistance, while giving it rich colors and patterns to attract consumers’ attention; or a lotion bottle with different shapes, the spraying process makes its appearance more colorful and stands out among many cosmetics.
According to market research data, in the cosmetic glass packaging market, products using spraying technology account for more than 70%, and this proportion is still increasing year by year. Consumers’ increasing attention to the appearance of cosmetics has prompted cosmetics companies to pay more attention to the surface coating process of glass packaging materials to enhance the competitiveness of their products.
The surface coating process of cosmetic glass packaging materials is a complex process that integrates technology and art. It gives glass packaging materials a unique appearance and excellent performance through spraying technology. From the principle and system composition of the spraying process to the basic process flow, each link is closely linked and jointly determines the final coating effect. In today’s fiercely competitive cosmetics industry, mastering advanced surface coating technology is of great significance to improving the quality and market competitiveness of cosmetic glass packaging materials. In the future, with the continuous advancement of science and technology and the increasing diversification of consumer demand, the surface coating process of cosmetic glass packaging materials will continue to innovate and develop, bringing more exciting products to the cosmetics industry.
I hope this article can help you gain a deeper understanding of the surface coating process of cosmetic glass packaging materials. If you have any other questions about the process or want to know more about it, please feel free to communicate with us.
The above blog analyzes the surface coating process of cosmetic glass packaging materials from multiple dimensions. If you have new ideas about the depth of content, case selection, etc., please feel free to tell me.
Entdecken Sie die Eleganz und Nachhaltigkeit von Glasverpackungen für Kosmetika! Erfahren Sie, wie Glasflaschen die Hautpflege schützen und sich an umweltfreundlichen Lösungen orientieren.
Discover why 62% of luxury skincare brands choose glass packaging: UV-blocking science, premium aesthetics, and eco-sustainability. Explore how glass bottles protect actives and elevate brand artistry.
Discover the unique properties of opal glass and its applications in cosmetic packaging, enhancing product quality, brand image, and protection with elegant textures.
Discover 10 expert tips to choose the best cosmetic bottles, ensuring quality, durability, and sustainability while enhancing your beauty routine effortlessly.
Entdecken Sie die Welt der Rohrdiffusoren und ätherischen Öle! Erfahren Sie, wie Sie die beste Glasflasche, das beste Schilfrohr und die besten Öle für ein entspannendes, aromatisches Zuhause auswählen.
Discover how rattan aromatherapy works and why glass bottles are the best choice for long-lasting scent, safety, and sustainable, elegant packaging.
Discover the top 10 woods for perfume caps, comparing texture, pros, cons, and price to help you choose the best material for stylish, high-quality packaging.
Explore cosmetic glass bottles—safety, eco benefits, types, coloring, mold costs, MOQ, and production tips—in one expert, data-rich guide.
Discover how to ensure high-quality silk screen printing on cosmetic and glass bottles with expert testing methods, defect analysis, and reliability standards.
Discover a complete guide to glass dropper bottles—from material and shape to customization and usage—for precise, durable, and high-end liquid packaging solutions.
Discover the unique properties of opal glass and its applications in cosmetic packaging, enhancing product quality, brand image, and protection with elegant textures.
WhatsApp uns