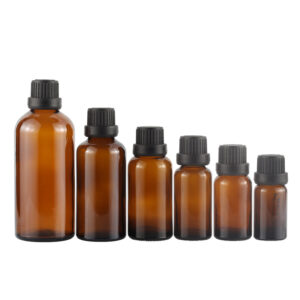
Nachrichten & Blog
Großartige Leistungen in der Wirtschaft werden nie von einer einzelnen Person erbracht. Sie werden von einem Team von Menschen vollbracht. Wir haben diese dynamische Gruppe von Menschen
In einer Zeit, in der der Wettbewerb in der Kosmetikindustrie immer härter wird, wird die Qualität der Kosmetikflaschen im Siebdruckverfahren immer wichtiger, Glasflaschen und andere Verpackungsmaterialien sind zu einem wichtigen Ausdruck des Markenimages geworden. Dieser Artikel konzentriert sich auf die Prüfung von Siebdruckprodukten, analysiert eingehend das Umfeld für die Prüfung von Siebdruckprodukten, häufige Defekte und Methoden zur Prüfung der Zuverlässigkeit und bietet Praktikern in der Branche eine Reihe systematischer und praktischer Lösungen für die Qualitätskontrolle von Siebdruckprodukten anhand detaillierter Daten, Tabellen und Abbildungen, die Unternehmen dabei helfen, die Produktqualität zu gewährleisten und die Wettbewerbsfähigkeit auf dem Markt bei kurzen Lieferfristen zu verbessern.
Die Prüfumgebung für Siebdruckteile hat einen entscheidenden Einfluss auf die Genauigkeit der Prüfergebnisse. Was die Lichtintensität betrifft, so muss die Prüfung unter Beleuchtungsbedingungen von 200-300LX durchgeführt werden, was der Lichtintensität einer 40W-Leuchtstofflampe in einem Abstand von 750MM entspricht. Unter dieser Beleuchtungsbedingung kann der Prüfer die feinen Defekte auf der Oberfläche des Siebdrucks deutlicher erkennen.
Elemente der Prüfumgebung | Besondere Anforderungen |
---|---|
Leuchtkraft | 200 - 300LX (entspricht einer 40W-Leuchtstofflampe in einer Entfernung von 750MM) |
Winkel zwischen Produkt und Blickrichtung | Etwa 45° |
Prüfzeit | Etwa 10 Sekunden |
Sichtweite für Oberfläche der Klasse A | 400MM |
Sichtweite für Oberfläche der Klasse B | 500MM |
Sichtweite für Oberfläche der Klasse C | 800MM |
Der Winkel der Produktplatzierung ist ebenfalls entscheidend. Die Oberfläche des Produkts sollte in einem Winkel von etwa 45° zur Blickrichtung des Prüfers stehen (siehe Abbildung 1), und die Beobachtungszeit sollte etwa 10 Sekunden betragen. Bei dieser Winkeleinstellung wird das Licht in geeigneter Weise auf der Produktoberfläche reflektiert, was es dem Prüfer erleichtert, verschiedene Fehler zu finden. Gleichzeitig ist der Abstand zwischen der Blickrichtung des Inspektors und der Oberfläche des zu prüfenden Produkts je nach der Beschaffenheit der Produktoberfläche unterschiedlich: Klasse A (direkt einsehbare Außenfläche): 400 mm; Klasse B (nicht einsehbare Außenfläche): 500 mm; Klasse C (schwer einsehbare Innen- und Außenflächen): 800 mm. Diese hierarchische Einstellung gewährleistet eine genaue Prüfung der verschiedenen Teile.
Beim Siebdruckverfahren von Kosmetikflaschen und Glasflaschen gibt es viele allgemeine Mängel, die sich direkt auf das Aussehen und die Leistung des Produkts auswirken.
Fremdkörper: Nach dem Siebdruck setzen sich leicht Staub, Punkte oder Fäden auf der Oberfläche der Beschichtung fest. Diese Fremdkörper beeinträchtigen nicht nur die Ästhetik des Produkts, sondern können auch bei der späteren Verwendung zu schlechten Erfahrungen für die Verbraucher führen.
Basisbelichtung: Die Grundfarbe wird freigelegt, weil die Farbe an der Siebdruckposition zu dünn ist. Diese Situation ist besonders offensichtlich beim Siebdruck von kosmetischen Verpackungsmaterialien mit hohen Anforderungen an die Farbkonsistenz, was die optische Gesamtwirkung des Produkts stark beeinträchtigt.
Druckfehler: Die Stelle, an der der Siebdruck erforderlich ist, wird nicht im Siebdruckverfahren bedruckt, was direkt zu fehlenden Produktinformationen oder unvollständigen Mustern führt und die Anforderungen an Markenlogo und Design nicht erfüllt.
Unscharfe/unterbrochene Linie: Bei einem schlechten Siebdruckverfahren sind die Siebdrucklinien und -muster ungleichmäßig dick, verschwommen, und die Wortzeilen sind teilweise voneinander getrennt. Dieser Fehler verringert den Wiedererkennungswert des Produkts und beeinträchtigt die Kommunikation des Markenimages.
Ungleichmäßige Siebdruckstärke: Aufgrund einer unsachgemäßen Siebdruckbearbeitung weist die Siebdruckschicht aus Punkten, Linien oder Mustern Dickenunterschiede auf. Dies beeinträchtigt nicht nur das Aussehen des Produkts, sondern kann auch zu einer ungleichmäßigen Farbhaftung führen und die Haltbarkeit des Produkts verringern.
Fehlausrichtung: Die Siebdruckposition ist ungenau und es kommt zu einem Versatz. Bei kosmetischen Glasflaschen mit strengen Designanforderungen zerstört eine falsche Ausrichtung die Koordination und Schönheit des Gesamtmusters.
Schlechtes Haftvermögen: Die Haftung der Siebdruckbeschichtung ist unzureichend, und der Siebdruckteil kann mit 3M-Klebeband abgeklebt werden. Dies bedeutet, dass der Siebdruckinhalt während des Transports oder der Verwendung des Produkts leicht abfallen kann, was die Produktqualität beeinträchtigt.
Lochkamera: Die Oberfläche der Beschichtung weist stecknadelkopfartige kleine Löcher auf, die nicht nur das Aussehen beeinträchtigen, sondern auch die Schutzwirkung der Tinte beeinträchtigen können.
Abschürfungen/Kratzer: Nach der Fertigstellung des Siebdrucks ist die Oberfläche zerkratzt oder verkratzt, weil sie nicht ausreichend geschützt ist, was die Qualität des Produkts mindert.
Farbe/Flecken: Farben, die nicht im Siebdruckverfahren hergestellt werden, bleiben auf der Siebdruckoberfläche haften, wodurch die Farbgleichmäßigkeit des Produkts beeinträchtigt wird und der visuelle Effekt verloren geht.
Farbunterschied: Im Vergleich zur Standard-Farbplatte weist der Siebdruck Farbabweichungen auf. In der Kosmetikindustrie ist die Farbgenauigkeit entscheidend für das Markenimage, und Farbunterschiede können dazu führen, dass die Verbraucher das Produkt in Frage stellen.
Um die Qualitätsstabilität von Siebdruckprodukten für kosmetische Glasflaschen in verschiedenen Umgebungen und Nutzungsszenarien zu gewährleisten, sind eine Reihe von Zuverlässigkeitstests erforderlich.
Hochtemperatur-Lagertest
Die Lagertemperatur ist auf + 66 °C eingestellt und die Lagerzeit beträgt 48 Stunden. Die Probe wird 2 Stunden lang bei Raumtemperatur gelagert, nachdem sie aus dem Ofen kommt. Die bedruckte Oberfläche darf keine Falten, Blasen, Risse oder Abblätterungen aufweisen, und der Farbglanz darf sich nicht wesentlich verändern. Dieser Test simuliert die Lagerung des Produkts in einer Umgebung mit hohen Temperaturen und prüft die Stabilität des Siebdrucks unter hohen Temperaturen.
Test bei niedrigen Temperaturen
Die Lagertemperatur beträgt - 40°C und die Lagerzeit 48 Stunden. Ebenso wird das Muster 2 Stunden lang bei Raumtemperatur gelagert, nachdem es aus dem Ofen kommt. Die bedruckte Oberfläche darf keine Falten, Blasen, Risse oder Abblätterungen aufweisen, und der Farbglanz darf sich nicht wesentlich verändern. Dieser Test dient dazu, die Toleranz des Siebdrucks bei niedrigen Temperaturen zu prüfen.
Test zur Lagerung bei hohen Temperaturen und hoher Luftfeuchtigkeit
Die Lagertemperatur/Luftfeuchtigkeit beträgt + 66°C/85%, und die Lagerzeit beträgt 96 Stunden. Nach dem Test wird das Material 2 Stunden lang bei Raumtemperatur gelagert, um zu prüfen, ob sich auf der bedruckten Oberfläche keine Falten, Blasen, Risse oder Abblätterungen bilden und keine offensichtlichen Veränderungen von Farbe und Glanz auftreten. Dieser Test simuliert eine raue Umgebung mit hohen Temperaturen und hoher Luftfeuchtigkeit, um die Feuchtigkeits- und Verformungsbeständigkeit des Siebdrucks zu bewerten.
Thermoschock-Test
Die Lagertemperatur wird zwischen - 40°C und + 66°C gewechselt, -40°C~+66°C ist ein Zyklus, und die Temperaturumwandlungszeit beträgt nicht mehr als 5 Minuten für insgesamt 12 Zyklen. Nachdem die Probe aus dem Ofen genommen wurde, wird sie 2 Stunden lang bei Raumtemperatur gelagert. Die Teile und die bedruckte Oberfläche dürfen keine Falten, Blasen, Risse oder Abblätterungen aufweisen, und es darf keine offensichtliche Veränderung der Farbe und des Glanzes auftreten. Der Thermoschocktest prüft die Anpassungsfähigkeit des Siebdrucks in einer Umgebung mit schnellen Temperaturschwankungen.
Siebdruck-/Tampondruck-Haftungstest
Der Zweck des Tests ist es, die Haftung von Siebdruck-/Tampondruckfarbe zu bewerten. Verwenden Sie 1,3M600 transparentes Klebeband oder transparentes Klebeband mit einer Klebrigkeit von mehr als 5,3N/18mm, kleben Sie das Klebeband auf die gedruckte Schrift oder das Muster der Probe, glätten Sie es mit den Händen, ziehen Sie das Ende des Klebebandes im 90-Grad-Winkel zur Testoberfläche nach oben, reißen Sie das Klebeband schnell ab und wiederholen Sie den gleichen Teil 3 Mal. Der Akzeptanzstandard besteht darin, die Oberfläche mit bloßem Auge zu betrachten, und die Schrift oder das Muster des Seiden-/Tampondrucks ist deutlich erkennbar, ohne sich abzulösen.
Reibungstest
Der Zweck ist, die Haftung von Farbe und Seiden-/Tampondruckfarbe auf der Beschichtungsoberfläche zu bewerten. Das Testgerät ist ein Radiergummi. Die Probe wird fixiert und mit einer vertikalen Kraft von 500 G und einem Hub von 15 mm hin und her gerieben. Jeder einzelne Strich ist ein Mal, und die Seiden-/Tampondruckschrift oder das Muster wird 50 Mal kontinuierlich abgerieben. Betrachten Sie die Oberfläche mit dem bloßen Auge. Die Abnutzung ist nicht bis zum Boden zu sehen, und der Seiden-/Tampondruck sollte klar und deutlich zu erkennen sein, um als qualifiziert zu gelten.
Prüfung der Lösemittelbeständigkeit
Isopropylalkoholtest: Nehmen Sie 1 ml Isopropylalkohollösung und tropfen Sie sie auf die besprühte Oberfläche oder die Seiden-/Tampondruckoberfläche der Probe. Nach 10 Minuten wischen Sie die Isopropylalkohollösung mit einem weißen Tuch ab.
Prüfung der Alkoholbeständigkeit: Tränken Sie einen Wattebausch oder ein weißes Tuch mit einer Alkohollösung (99%) und wischen Sie mit einem Druck von 1 kg und einer Geschwindigkeit von 1 Umdrehung pro Sekunde 20 Mal an der gleichen Stelle des Musters hin und her, an der Schrift und Muster aufgedruckt sind. Nach dem Abwischen sollte die gedruckte Schrift oder das Muster auf der Oberfläche der Probe deutlich sichtbar sein, und die Farbe sollte nicht an Glanz verlieren oder verblassen, um qualifiziert zu sein.
Daumentest
Die Versuchsprobe muss mehr als 5 PCS umfassen. Nehmen Sie das Muster, legen Sie den Daumen auf das gedruckte Bild und reiben Sie es 15 Mal mit einer Kraft von 3+0,5/-0KGF hin und her. Das gedruckte Muster des Produkts darf keine Lücken, unterbrochene Linien und eine schlechte Tintenhaftung aufweisen, sonst wird es als untauglich eingestuft.
75% Alkoholtest
Zu den Bedingungen gehören mehr als 5 PCS Versuchsmuster, weiße Baumwollgaze, 75%-Alkohol und 1,5+0,5/-0KGF-Halterung. Binden Sie weiße Baumwollgaze an den Boden der 1,5KG-Halterung, tauchen Sie sie in 75%-Alkohol und bewegen Sie sie 30 Mal (etwa 15 Sekunden) auf dem gedruckten Muster hin und her. Das gedruckte Muster des Produkts darf nicht abfallen, Lücken und unterbrochene Linien aufweisen oder eine schlechte Tintenhaftung haben. Helle Farben sind erlaubt, aber das gedruckte Muster sollte klar und nicht verschwommen sein, andernfalls ist es untauglich.
95% Alkoholtest
Ähnlich wie beim 75%-Alkoholtestverfahren wird 95%-Alkohol verwendet, und die experimentellen Beurteilungskriterien sind die gleichen, um die Toleranz des Siebdrucks in verschiedenen Alkoholkonzentrationen zu gewährleisten.
810 Bandprüfung
Bei mehr als 5 PCS Testmustern kleben Sie das 810er Band vollständig auf den Siebdruck, ziehen das Band dann schnell in einem 45-Grad-Winkel nach oben und messen dreimal hintereinander. Das gedruckte Muster des Produkts darf nicht eingekerbt oder gebrochen werden.
3M600 Klebebandtest
Bei mehr als 5 PCS Versuchsmustern kleben Sie das 3M600 Klebeband vollständig auf den Siebdruck und ziehen Sie das Band in einem 45-Grad-Winkel schnell ab. Es ist nur ein Test erforderlich. Das gedruckte Muster des Produkts darf nicht eingekerbt oder gebrochen werden.
250 Bandtest
Bei mehr als 5 PCS Versuchsmustern kleben Sie das 250er Klebeband vollständig auf den Siebdruck, und ziehen Sie das Klebeband dreimal hintereinander in einem Winkel von 45 Grad ab. Das gedruckte Muster des Produkts darf nicht eingekerbt oder gebrochen werden.
Benzin-Wischtest
Die Bedingungen sind mehr als 5 PCS von experimentellen Proben, weiße Baumwollgaze, Benzinmischung (Benzin: 75% Alkohol = 1:1) und 1,5+0,5/-0KGF Werkzeug. Binden Sie weiße Baumwollgaze an die Unterseite der 1,5KGF-Vorrichtung, tauchen Sie sie in die Benzinmischung und fahren Sie 30 Mal (ca. 15 Sekunden) auf dem Druckmuster hin und her. Das aufgedruckte Muster darf nicht abfallen, Lücken, unterbrochene Linien, schlechte Farbhaftung usw. aufweisen. Die Farbe kann hell sein, aber das gedruckte Muster sollte klar und nicht verschwommen sein, andernfalls ist es untauglich.
N-Hexan-Wischtest
Bei mehr als 5 St. Versuchsmustern binden Sie weiße Baumwollgaze an den Boden der 1,5KGF-Vorrichtung, tauchen sie in n-Hexan-Lösung und fahren 30 Mal (etwa 15 Sekunden) auf dem gedruckten Muster hin und her. Das aufgedruckte Muster darf nicht abfallen, Lücken, unterbrochene Linien, schlechte Farbhaftung usw. aufweisen. Die Farbe kann hell sein, aber das gedruckte Muster sollte klar und nicht verschwommen sein, sonst ist es untauglich.
Die Inspektion von Siebdruckprodukten für kosmetische Flaschen aus Glas ist ein wichtiges Element zur Gewährleistung der Produktqualität. Von der Festlegung einer strengen Prüfumgebung über die genaue Identifizierung allgemeiner Fehler bis hin zu umfassenden Zuverlässigkeitsprüfungen - jeder Schritt hat einen wichtigen Einfluss auf die Produktqualität. Mit dem in diesem Artikel vorgestellten Prüfschema können Unternehmen die Qualität von Siebdruckprodukten systematisch kontrollieren und sicherstellen, dass die Produkte den Anforderungen von Marken und Verbrauchern in Bezug auf Aussehen und Haltbarkeit entsprechen. Da die Kosmetikindustrie die Lieferfristen für Verpackungsmaterialien immer weiter verkürzt, wird die Beachtung der Siebdruckprüfung den Unternehmen helfen, die Wettbewerbsfähigkeit ihrer Produkte zu verbessern und ein gutes Markenimage aufzubauen. Im eigentlichen Produktionsprozess sollten die Unternehmen diese Prüfmethoden entsprechend ihren eigenen Produkteigenschaften sinnvoll einsetzen und den Prüfprozess kontinuierlich optimieren, um ihn an Marktveränderungen und Kundenbedürfnisse anzupassen.
Yafeng Packaging hat sich verpflichtet, eine erstklassige Qualitätssicherung zu bieten. Wir haben ein strenges Qualitätskontrollsystem eingeführt, insbesondere für die Qualitätsprüfung des Siebdrucks. Von der Inspektionsumgebung bis hin zu den umfassendsten Zuverlässigkeitstests wird jeder Schritt in Übereinstimmung mit internationalen Standards durchgeführt. Unser professionelles technisches Team und unsere fortschrittlichen Prüfgeräte stellen sicher, dass jede Produktcharge die Erwartungen unserer Kunden erfüllt oder übertrifft. Das macht uns zu Ihrem zuverlässigen Partner für hochwertige Kosmetikverpackungen.
Entdecken Sie das Sprühbeschichtungsverfahren für kosmetische Glasverpackungen, einschließlich Techniken, Vorteile und Tipps zur Steigerung der Produktattraktivität und des Markenwerts.
Finden Sie heraus, ob Parfümflaschen recycelbar sind und erfahren Sie, wie Sie sie recyceln oder wiederverwenden können. Ein Leitfaden zur umweltfreundlichen Entsorgung von Parfüm und zu nachhaltigen Optionen.
Informieren Sie sich über die Unterschiede zwischen Sandstrahl-, Mattierungs- und Sprühbeschichtung für Kosmetikflaschen aus Glas. Erfahren Sie mehr über die Anwendungen, die Kosten und darüber, was am besten zu Ihrer Marke passt.
Entdecken Sie die Geheimnisse der Parfümkonservierung: Wie sich Flaschendesign und Temperaturkontrolle auf die Duftqualität auswirken. Erfahren Sie Expertentipps für die optimale Lagerung.
Erforschen Sie die Nachhaltigkeit von Glasverpackungen, ihre Wiederverwertbarkeit und die Vorteile für die Umwelt.
Entdecken Sie, wie die Sprühbeschichtung Hautpflege- und Parfümverpackungen aufwertet, indem sie das Erscheinungsbild, die Markenidentität, die Haltbarkeit und die Sicherheit mit fortschrittlicher Technologie verbessert.
Informieren Sie sich über individuelle und Standardflaschen für Hautpflegeverpackungen. Erfahren Sie in diesem ausführlichen Leitfaden, wie die Lösungen von Yafeng die Markenidentität, Qualität und Effizienz steigern.
Entdecken Sie, wie Farbverlaufsspray kosmetische Glasflaschen verwandelt, das Markenimage verbessert und die Produktattraktivität steigert - mit Expertenwissen von Yafeng Packaging.
Entdecken Sie, wie die Rattan-Aromatherapie funktioniert und warum Glasflaschen die beste Wahl für einen lang anhaltenden Duft, Sicherheit und eine nachhaltige, elegante Verpackung sind.
Entdecken Sie die 10 besten Hölzer für Parfümkappen und vergleichen Sie Beschaffenheit, Vor- und Nachteile sowie den Preis, damit Sie das beste Material für eine stilvolle, hochwertige Verpackung wählen können.
Informieren Sie sich über kosmetische Glasflaschen - Sicherheit, ökologische Vorteile, Typen, Färbung, Formkosten, MOQ und Produktionstipps - in einem sachkundigen, datenreichen Leitfaden.
WhatsApp uns